|
|
第五节 覆铜板用压机 |
|
|
|
压机是制造覆铜板最终成型的关键设备,压机精度的好坏及合适的工艺参数对板材品质起着至关重要的作用。由于覆铜板的压制过程,是将一定数量的半固化片和涂胶铜箔夹在不锈钢板工装中,置于加热板间,同时有许多层在压机中按工艺要求完成压制,所以又称层压机;又由于在压制过程中还必须进行加热压制成型,又称为热压机。
按照覆铜板压制过程处于非真空或真空状态,覆铜板压机可分为非真空压机(或开放式压机)和真空压机;按加热媒质的不同,又可分为蒸汽加热和导热油加热压机;按所能压制的覆铜板的大小,还可分为单幅压机和双幅压机。在上世纪90年代之前,压机一般采用单幅非真空压机,用蒸汽加热。90年代之后,多采用真空压机,用导热油加热,双幅压机更多地被采用。
一、覆铜板压机的结构原理及相关计算
覆铜板压机结构的简单原理如图3-5-1所示。
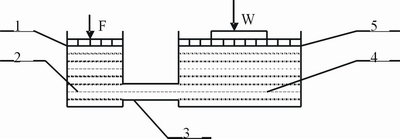
1,5—活塞; 2,4—液压缸; 3—管道
图3-5-1 热压机液压的简单原理图
图中有两个直径大小不同的液压缸2和4。缸内各有一个与内壁紧密配合的活塞1和5,假设活塞能在缸内自由(无磨擦力)滑动,而液体又不会通过配合处产生泄露。缸2、4的下腔用一管道3相连通,其中都充满液体。液体在密闭容器内,如果活塞5上有重物的力施加W,则当活塞1上施加的F力达到一定大小时,就能阻止重物W下降,也就是密封容器中的液体可以传递力,当活塞1在F力作用下向下运动时,重物W将随之向上运动。所以,密封容器中的液体不但可以传递力,还可以传递运动。在传递过程中,密封容器的液体受到挤压产生一定压力,液体压力又作用在活塞上,活塞1单位面积上受到的压力为 
活塞5单位面积上受到的压力为 
A1和A2分别为活塞1、5的面积。
根据流体力学的帕斯卡定律:“平衡液体内某一点的液体压力等值的传递到液体内各处”。因此,则有: 
也就是说输出端的力和输入端的力之比等于两活塞面积之比。上图热压机液压的简单原理图中的小活塞相当于热压机的高压泵,大活塞相当于热压机的工作活塞。由以上公式可以得出热压机总吨位计算式: 
式中:P总为热压机总吨位;
P—油缸中最大压力(N/M2);
A2—活塞面积(m2)。

式中:D为活塞直径(m); N为活塞个数。
使用热压机时,因加压时,除去消耗于工作活塞克服的磨擦阻力等损失外,还有漏油跑压现象。因此热压机总压力一般要比理论总压力小10—15%。
压机的结构示意图如图3-5-2所示。主要有机架、上顶板、热压板、下顶板、油缸等组成。当然还有加热、冷却系统、加压系统、贮油箱等,真空压机还有真空系统。目前覆铜板用压机的机架,一般都为框架结构,其结构简单、制造方便,中、小型压机,多为立柱式结构,其结构复杂,制造较难;热压板内有孔道,孔道内通入热油或蒸汽进行加热。热压板的厚度和孔道的布置与排列,对其表面各点温度均匀性有直接影响;油缸有单缸、双缸、四缸和六缸多种形式,覆铜板用热压机,大都为柱塞式油缸,它通过液压系统给压机提供压力。
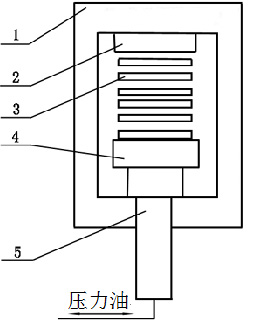
1-机架;2-上顶板;3-加热板;4-下顶板;5-油缸
图3-5-2 压机结构示意图
压机的主要技术性能,见表3-5-1。
表3-5-1 压机的主要技术性能
名 称 |
单位 |
1500 吨压机 |
2000 吨压机 |
最大压力 |
牛顿(N)
吨(T)
|
147×107
1500 |
196×107
2000 |
最大单位压力 |
兆帕(Mpa)
工程大气压(kgf/cm2)
|
12.3
125 |
7.8
80 |
热压板尺寸(长×宽×高) |
毫米mm |
1300×1200×60 |
2200×1150×62 |
层数 |
层 |
20 |
20 |
每层空距 |
毫米mm |
100 |
150 |
压力油缸直径/个数 |
毫米/个mm/个 |
Φ400/4 |
Φ300/8 |
油泵最高极限输出压力 |
兆帕(Mpa)
工程大气压(kgf/cm2)
|
29.4
300 |
35.3
360 |
对于热压机操作者,应该掌握热压机表压计算:
(1)常用压强(单位面积上受到的压力)单位的换算:
压强的国际单位制为帕(帕斯卡)或兆帕,1帕(pa)=1牛顿/米2 (N/m2), 1Mpa=106pa,1kgf/cm2=9.8×104 N/m2(牛顿/米2或pa)≈0.1 Mpa(兆帕), 1Mpa=10.2kgf/cm2
常用压力单位换算:1千克(kg) =9.8牛顿(N) 1牛顿(N)=0.102千克(kg)
其它非法定计量单位的换算,详见本书附录《常见非法定计量单位和换算系数》。
(2)计算公式
最大表压法公式:已知压机的吨位和相应吨位最大表压,则可用下式:

活塞面积法公式:已知活塞直径和板的受压面积,即可用下式求表压:
 其中活塞面积=πR2 .n 。π为圆周率3.14159 ,R为活塞半径m,n为活塞个数
二、层压系统分述
层压系统一般都是由压机、上料架(也称装板机)、下料架(也称卸扳机)、送料架(车)和操作系统组成,如图3-5-3。
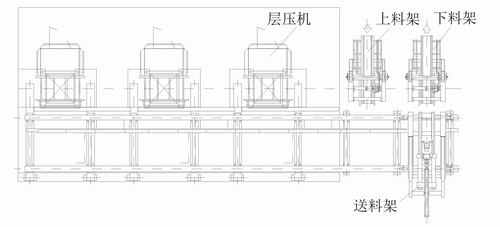
图3-5-3 层压系统
(一)、层压机组成
层压机一般由四大部份组成(见图3-5-4):油缸和液压系统、加热板和加热冷却系统、真空系统、控制系统
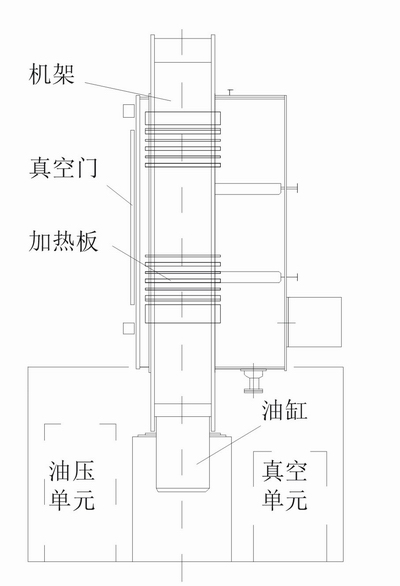
图3-5-4 层压机
1、油缸和液压系统 该系统根据工艺要求提供层压过程中所需的不同压力。油缸在压机位置有底部和顶部2种放置方式:
(1). 油缸置于底部 这种方式是传统方式,它的最大优点是可以采用单油缸实现很大的压力,对于大压机压力高达1000吨,油缸活塞一般都在Ф650mm左右,在这种情况下,油缸置于压机底部,整个压机重心下沉,是一种合理设计。但由于这种大压机的开口数都比较多,油缸行程及总长度比较大,如果油缸装在地面上则压机最下面一个开口就很高,不利于操作和维护,所以这种压机其油缸必须置于地坑之中,安装之前要先挖地坑。
1UP(单幅覆铜板,即覆铜板厂对覆铜板板不用分切。)压机大多采用单油缸,而对于2UP(双副覆铜板,覆铜板厂必须对覆铜板一切为二。)压机则可能用2个或2个以上大油缸。选用多大或多少个油缸主要根据三个因素确定:产品所需压力、油压系统元器件本身所能承受的压力、设备制造商本身的加工能力。
(2). 油缸置于压机顶部 这种方式以美国OEM为典型,将本来在压机底部可以由一个油缸来完成的压力,在顶部要由4个油缸来实现。这种方式最大的优点就是无论大小压机均不用挖地坑,可以直接在地面上将压机就位安装好;而最大缺点就是油缸置于压机顶部,维修、保养比较困难。
(3).油缸的结构(见图3-5-5) 油缸主要由.缸体、.活塞、密封件、导向套四大部份组成。
①缸体 缸体一般选用45#钢制造,但必须对钢材调质处理到HBS241~285。
②活塞 活塞采用耐磨铸铁制造而成,表面不仅要光滑,而且要耐磨。目前进口压机如KITAGAVA和SIEMPKAMP之活塞加工完全达到镜面级0.05μ而且硬度也达到HRC48以上。
③导向套 导向套材料一般为耐磨青铜,其表面粗糙度为0.63μ,利用液压油润滑导向套。
④密封与防尘装置 采用“Y”型密封圈。
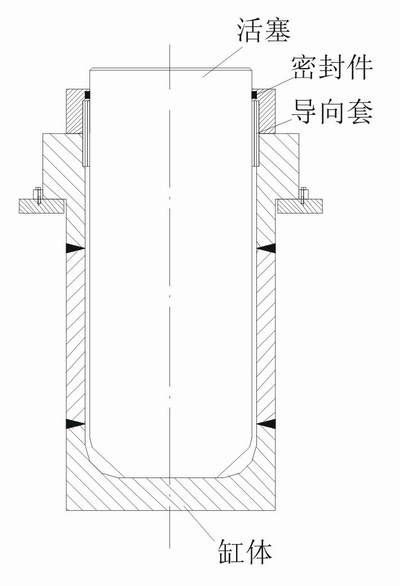
图3-5-5 油缸结构
(4). 层压机的液压系统 产品所需要的压力及压力的稳定性均匀,都是通过液压系统来实现,所以液压系统是否可靠对压机非常重要。制造覆铜板层压机液压系统基本上大同小异,都是为了2个目的:A-正常工作状态下精确控制液压系统的压力;B-在出现异常情况时,系统能保压甚至能手动补压。这里我们以图示3-5-6液压系统为例来概述液压系统之工作原理。
液压系统主要由高低压泵、方向阀、比例调压阀、安全阀、单向阀、油箱、过滤器等元器件组成。
①高低压泵 层压机在合模时由于油缸大,需要泵提供大流量、低压力的液压油;但当合模到位后,油缸仅需要小量油加压或保压,如果仅用一个油泵,既需要流量大又需压力大,对泵的功率必须选很高,同时液压油在高压下溢流,容易发热,严重时会影响液压元件的使用性能。所以目前所有的大中型压机均采用高、低泵分开,低压泵提供油缸所需流量,高压泵提供油缸所需油压。
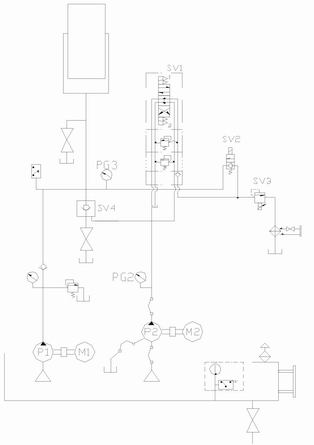
P1-低压泵 P2-高压泵 SV1-换向阀电磁阀
SV2-通断阀 SV3-比例调压阀 SV4-开模单向阀
图3-5-6 液压系统
② 方向阀 方向阀SV1用于压机合模和开模,SV2则用于紧急状态下,如停电情况下油缸保压。
③ 比例调压阀 层压机液压系统的压力可以任意设定,这是由比例调压阀来实现的。其原理是DCP给功率放大器一个信号,通过功率放大器给比例调压阀不同的电压,比例调压阀按照电压(或电流)值调定某一压力值,当油路压力超过这个值时,油会溢流回到油箱,于是保证了油路压力为设定值。
④ 单向阀和液控单向阀 该系统单向阀有4个之多,这些单向阀均是为了防止油缸液压油泄漏,其中单向阀SV4是液控单向阀,必须在SV1线圈2有电时,单向阀SV4才能动作打开,把主油路单向阀打开,活塞在自重作用下而下降,实现压机开模。
2、加热板和加热冷却系统
除利用铜箔加热方式和连续层压外,其余压机对产品加热均需加热板。
(1).加热板结构 加热板结构大致有如下几种,见图3-5-7。
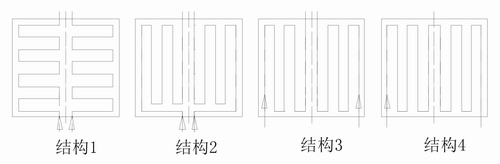
图3-5-7 加热板结构
其中双回路加热板多用于大压机,而单进单出加热板一般用于中小型压机,或者是对加热板温度均匀性要求不高的压机。大多数加热板的厚度是60mm,日本KITAGAWA压机(1UP)加热板只有50mm厚;加热板内孔孔径一般为φ22-φ32 mm。
(2).加热板精度 压机热板精度对产品起着重要作用,目前世界上主要压机设备供应商其加热板平面度均在0.04-0.05mm/m之间。为有效保护加热板表面,在加热板上表面上加装一块硬度较高且耐磨的保护板。在加热板前端有托滚,以利于BOOK送入压机,在加热板侧有导向轮,以使BOOK放正在加热板中间。
(3).加热方式 压机加热方式有蒸汽加热、导热油加热、.电加热及铜箔加热4种
① 蒸汽加热 早期压机加热用蒸汽加热,用水冷却,其结构和原理见图3-5-8。
蒸汽加热系统构成 由进蒸汽阀、进冷水阀、回锅炉阀、疏水阀、排水阀、排蒸汽阀等构成。
控温原理 加热板控温通过装于热板上的热电偶检测热板温度,控制进蒸汽阀的开度大小来控制加热板温度。在加热过程中,热板中的积水回流到疏水阀处,当积水达到一定程度后,疏水阀自动打开,将积水排回锅炉。
加热板冷却 通过冷却塔水池的水来冷却,在压机热板通冷却水之前,必须将热板中的蒸汽预先排空,再通入冷却水,否则会产生水气撞击。
蒸汽加热的优缺点:压机用蒸汽加热,管路比较简单,也无需再配热源输送动力,只要控制蒸汽进入热板的多少就可以控制热板之温度。同时热板或管路出现漏水现象,维修起来比较方便。设备运行较为安全,投资少。但用蒸汽加热存在一些严重缺点:热板升温速度慢(最高温度一般只达到160—170度),温度随蒸汽压变化难以稳定,热板板面温度分布均匀性不理想;对覆铜板的产品质量不利。蒸汽的冷凝水对不同层加热板温差影响比较大;管道压力大,蒸汽在190℃时压力有15kg/cm2,如果我们要求提高蒸汽温度,势必要提高蒸汽压力,这就对管道、阀门等提出更高要求。采用蒸汽加热,比较浪费能源,在加热和冷却过程中存在蒸汽赶水,也存在排放蒸汽,这两者都造成热能浪费。
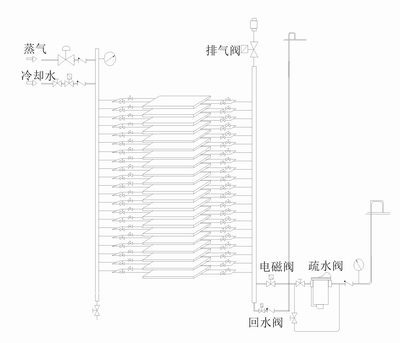
图3-5-8 压机蒸汽加热结构
② 导热油加热 导热油加热压机可分为冷热一体和冷热分开两种方式。
加热系统,这套系统主要由热油锅炉系统和温控组两大部份组成。热油锅炉提供压机所需要的热能,由于压机在升温时短时间需要大量热量,而在保温或降温时压机仅需要少量甚至不需要热量,按压机最大热量需求功率来选锅炉,势必造成锅炉太大,所以压机热油系统需要配备蓄热罐,既可以减少锅炉功率,又可在锅炉有故障时有储备热量供给。
冷却系统(冷热一体),在冷却时蓄热罐中的导热油和压机中的热油会自动隔断,已经存在于压机中的导热油通过热交换器中的冷却水带走热量,加热板冷却是一个平稳的过程,这种方式对热板和产品都有利。但对于热交换器来说。由于高达200℃以上的导热油和低温的水进行交换,这样对交换器提出了很高要求,交换器的质量一定要好。
为了节约用水,现在冷却方法一般采用循环水冷却。
采用导热油加热具有下述优点:热板升温速度快(最高温度一般可达到200度),加热冷却时间短,提高压机利用率,每台压机产量约增加30%;加热板温度均匀,层间温度也均匀,甚至可以实现热板温度相差在±1.5℃內;可使覆铜板板面颜色不一致的“色差”问题得到较好解决;管道压力小,温控稳定,安全可靠,不容易腐蚀管道;温度可以升到很高,导热油可耐340℃高温,锅炉可以烧到300℃,正常使用温度可达270℃;导热油循环使用,无废水、无污染等问题,相对蒸汽加热要节能约50%,投资也较少,施工方便,系统便于全自动化控制;导热油加热的最大缺点就是管道相对复杂,需要油泵和阀门较多,油路接管要求严格,必须设计导热油加热、输送系统。
③ 电加热 用发热棒直接加热加热板,这种方式热板温度不好控制,温差较大,而且耗能较高,所以用电加热一般用于小型压机或试验用压机。
3、真空系统 压机采用真空技术的主要功能,就是在真空状态下,能将半固化片固化过程中产生的气泡更容易排出去,降低压制覆铜板板的压力,从而减少覆铜板的翘曲,提高覆铜板的质量。玻璃布基覆铜板几乎都采用真空压制,纸基覆铜板现在也越来越多地采用真空压制。
真空系统主要有如下要求:
(1). 真空室完全密封,不仅要求压机框架有足够强度和良好的密封性能,而且要求真空门.维修门等具有良好的密封性能;
(2). 抽真空管道及阀门具有良好的密封性能;
(3). 真空泵具有良好的性能,有足够的抽真空能力。目前压机对真空度要求很高,抽真空能力一般要在5-6min可以抽到30torr,极限真空可以抽到10torr以上。在真空泵的选型上大多数压机包括KITAGAWA、OEM、ACCUDYNE等压机均采用BUSCH公司生产的真空泵,BUSCH泵性能不错,结构简单,维修方便,但由于BUSCH泵是叶片泵,需要良好的润滑性能,而抽真空时空气中的水份容易积在真空泵油中,造成真空泵中油容易乳化甚至碳化,这就使得叶片和泵体润滑性能减弱,形成恶性循环,造成叶片容易磨损,油气分离器破损。这就要求对真空泵进行精心维护,特别是要加强对真空泵的排水工作。
另外一种真空泵就是水环式真空泵,这种泵最适合层压机抽真空。因为它不存在润滑及腐蚀两个问题,只是这种真空泵使用条件比较高,需要冷却水且要在5℃-15℃之间,而且水环泵抽真空需要电机功率也比较大,价格又贵,所以目前选用真空泵从购买成本考虑大多仍选用BUSCH泵。
4、控制系统 层压机主要要控制压力、温度2个参数,有的压机还控制真空度。压力、温度2个参数变化都是用电脑控制, KITAGAWA压机除用电脑控制外,还可以用DCP来控制。
(二)、上料架和下料架
1、结构 由升降机构、输送机构和托架组成。
2、原理 上料架通过升降机构将1个个叠合好的BOOK(即装入两块加热板之间待压制的10张以上覆铜板料,每张覆铜板料都夹装在两块不锈钢板工装中。)提升到不同层高度,再由输送机构将BOOK送进上料架的托架上,上料架放料过程是由上往下进行的。下料架则是由下而上由传送机构和提升机构将一个个BOOK从下料架取下来,送到回流线拆板机去拆板。
(三)、送料车
1、功能 将上料架的BOOK送到压机,又将压合好的板由热压机送到冷压机或将冷压机或冷热一体压机冷却好的板送到下料架。
2、结构及原理 送料车采用AC马达驱动横移,只有当送料车准确对准压机或上下料架,并由定位销完全准确锁紧后,送料车才能由推臂和提钩取送BOOK。提钩有单钩和双钩之分,双钩取送BOOK更准确,在提钩钩住托板后,由推臂来完成送取BOOK。早期压机推臂很多都用丝杆或齿轮齿条来完成推拉动作,现在基本上都用油缸来实现推拉动作。
(四)、操作系统 对于压机、上料架、下料架、送料车所有动作,均采用PLC控制,可以全自动完成所有动作。
(五)、压机精度的测试
对压机性能的评定,不同设备供应商和设备使用厂家都有不同方法,测热板温度的方法大家基本一样,测热板均匀性的方法则各有不同。
1、压力纸测定法 这种方法就是在热板与热板中间放上下各2张牛皮纸,牛皮纸中间放一张压力应变纸(常态下白色),在合模压力状态下,看压力纸变颜色的程度(变为红色,颜色越深压力越大)来定性分析热板均匀性。
2、复写纸测定法 这种方法与压力纸方法一样,只是将压力纸换成了复写纸,也是一种定性测试方法。
3、铅条测定法 这种方法采用铅条放在热板与热板之间,左中右各放一条,在合模压力作用下,铅条厚度发生变形,再将铅条从热板中间取出,用千分尺测量铅条前中后不同点的厚度,这样就可以定量测得加热板均匀性的数据。
4、温度均匀性测量 热板层间温度绝大部分压机都有电脑显示,无须测试。只是同一块热板温度均匀性需测试。测量方法:一般先预叠一个BOOK,这个BOOK仅需托板、盖板和适量的牛皮纸,将九条热电偶线埋入牛皮纸中间(分布在板的角或中心点),并将热电偶线接入压机预留的九个测温接口或自备的温度测试仪,这样压机电脑或测试仪就可以显示并记录同一块热板不同点的升温情况,在热板温度稳定后,可以看到要测的九点温差情况。
三、覆铜板压制系统选配
1、普通的覆铜板用热压机系统
覆铜板的压制过程,必须将每张覆铜板所用的半固化片和铜箔,夹在两块不锈钢板工装之间,再将10张以上覆铜板的材料装入两块加热板间,大型覆铜板压机在上下顶板间,有20-40层加热板的档间,即每完成一次(一般称一模)压制,就可制造出200-400多张覆铜板。所以仅装板、卸板工步,至少需配置装板机和卸扳机。当覆铜板产量不大时,一台压机配一台装板机和一台卸扳机,其它物料传送、叠配料、钢板工装传送、清洗等等工步,都由手工完成。这种配置如图3-5-9所示。
1-液压系统;2-卸料车;3-链式运输机;4-卸机推拉机;5-卸板机;
6-热压机;7-装板机;8-装机推拉机;9-链式运输机;10-装料车
图3-5-9 普通的覆铜板用热压机系统
2、“两热一冷”压机组
图3-5-9的系统,覆铜板压制过程的加热和冷却都在同一台压机中完成,这样生产效率低、热量损失大,不适合规模化大生产。当工厂生产达到了一定规模时,一般有多台压机同时使用,采用“压机组合”的方式进行压制生产。前面图3-5-3所示的就是一种组合形式。
目前比较流行的搭配方案一般以三台压机一组配一条回流线。在覆铜板的压制过程中,根据工艺要求有加热和冷却时间的规定,而同一规格产品热压成型所需时间长,冷却定型所需时间较短(加热时间大约是冷却时间的一倍)。根据这一工艺要求的特点,就衍生了“两热一冷”压机组合(2台热压机配1台冷压机)。这样3台压机升温、保温、冷却可以相互错开,不会对能源要求提出更高要求。欧美压机供应商从节约能源角度出发,一般采用 “两热一冷”机组,如图3-5-10所示。但日本和中国台湾的设备供应商,特别是日本方面的设备供应商,以满足覆铜板制造工艺要求为前提,也有采用冷热一体压机的。
冷热分开与冷热一体比较,冷热分体有下述优势:由于热压机始终保持热板在比较热的状态,不会浪费热能,因而更加节能;冷压机技术要求相对偏低,加工制造容易一些,同样三台压机, 2热1冷比3台冷热一体压机投资成本低。 
1、移动推拉板车 2、装板机 3、1号真空热压机 4、真空系统 5、1号液压系统 6、2号液压系统 7、2号真空热压机 8、热油系统 9、冷却系统 10、冷压机液压系统 11、冷压机 1、2卸板机 13、移动道轨
图3-5-10 覆铜板用“两热一冷”压机组
“两热一冷”压机组中,两台热压机和一台冷压机共用一套移动推拉板车。以20层压机为例,对组合设备运行简介如下:按工艺要求将半成品叠合后逐层装入装板机2中,装完20层为一模。然后开启移动推拉板车,将这一模装好的板连同运载板一起从装板机中拉入移板车上。调整移动推拉板车方向对准压机3或压机7,将车上的板推入压机中按工艺要求进行热压成型。成型后的模板再由移动推拉板车拉出,并及时推入冷压机11中进行冷却定型。冷却工序完成后,再由移动推拉板车拉出,并及时推入卸板机12中逐层卸板。整个流程中所使用的设备(装板机2、移动推拉板车1、热压机3、热压机7、冷压机11、卸板机12及有关付属设备)统称“两热一冷”压机组合。除图中所示外,还有温度、压力指示与控制系统,真空系统、空压系统。如果电气部分采用PC装置,则可实现压制全过程的自动控制,从而确保产品科学地最优化生产。
综上所述“两热一冷”压机组合有以下特点和要求:
(1)特点 :
①产品的加热和冷却分别在热、冷压机中进行,生产效率和产量相对较高。
②节约热源(热压机中的热压板不需要冷却)。
③在规模化生产车间的布置中,设备占地面积少,投资相对少一些,同时也容易实现自动化流水作业生产。
④设备配置较为合理,利用率高。
(2) 要求:
①产品的工艺:加热时间必须大于或等于冷却时间的一倍。
②三台压机操作标高、层间距、层数必须相同。 |
|
|
|
|
|
|
热点新闻 |
|
|
|