|
|
第七章 第五节 压制成型技术 |
|
|
|
覆铜板压制成型是在层压机上完成的。粘结片在层压机中受热受压先软化、熔融,高分子物变为粘流态,随着温度逐步升高和时间增加,树脂开始发生固化反应,粘度逐步增大,当到达凝胶点时,粘度迅速增大。双氰胺是一种潜伏性固化剂,在有促进剂存在下70℃开始缓慢和环氧树脂起固化反应,到达120℃以后,反应速度加快。到150~155℃反应达高峰。在此过程中,高分子物逐步交联固化,高分子物由粘流态转入粘弹态,当温度到达175℃以后,固化反应基本完成,粘结片与铜箔牢固粘合,产品完全硬化而成覆铜板。因此,覆铜板层压成型必须供热,以促使固化反应进行。同时必须加压,环氧玻纤布覆铜板其固化进程虽然是加成型聚合反应,但由于双氰胺吸潮性及多种因素,固化过程或多或少仍有一些水份、低分子物存在。因此需要加压排除这些水份、低分子物,以保证产品层间牢固粘合,而且没有孔洞、气隙存在。加压尚可增加粘流态下树脂渗入玻纤间隙,有利于提高制品密度、制品表面平滑性及基板与铜箔粘合程度。由于粘结片上的水份、低分子物量很少,所以压力不必像纸基覆铜板那样大。层压升压过程也不必“放气”。当使用层压机压制产品时,高真空状态下低分子物,水气更易逸出,因而可以用比较低的层压成型压力。当固化反应完成以后,又必须将其逐步降温冷却,以取出产品。因此,层压过程有加热、加压、冷却过程,即层压机应具有加热、加压冷却功能。
层压机详见第三章第三节。本节结合层压工艺和操作再作进一步阐述。
一、层压机结构
覆铜板生产用层压机均为多开口形式,以提高单机生产能力。较小型的有十来个开口,大型的有高达四十几个开口。层压机热压板面积多数都采用略大于单张产品面积。大型的有可生产二张产品面积,甚至可生产三张产品面积。多数层压机采用液压缸在机架下方的“上顶式”层压方式。压缸有单缸、双缸、四缸、六缸甚至八缸。也有少数压机液压缸在机架上部的“下压式”层压方式,这种形式只用在小型压机。也有一些大型压机液压机构在机架上部,但液压过程是采用“上拉式”,将压机最下层底盘由四根液压柱往上提拉,其压制过程和“上顶式”相同。层压机的框架,小型压机多数用四根立柱作支撑。大型压机则多为框架式结构,特别是真空压机,更需采用框架式结构,才能做成密闭式。“下压式”及“提拉式”层压机优点是设备安装时不需挖地坑来安放液压缸。设备安装比较简单、快捷。对于单缸和多缸液压缸特性比较,采用单缸要达到相同吨位压力,缸体的直径必须做得很大,且精度较高,机械加工难度相应加大。采用多缸,要达到相同吨位压力,则缸体直径可以做得比较小,机械加工较容易。采用单液压缸,压力分布均匀性较好调节,采用多液压缸,要使每个缸出力完全相同较难调节。
早期液压机都是非真空式的,因此吨位压力都设计得比较高,以适应层压产品性能要求。随着对覆铜板性能要求逐步提高,出现真空层压技术和真空层压机。
(一)真空层压机
覆铜板热压成型压力越大,产品内应力也越大,导致产品翘曲度也较大,热压过程中流胶偏多,也影响产品诸多性能。真空层压法的出现,使产品成型压力大大降低。真空层压法分抽压法及舱压法。
1.真空抽压法
真空抽压法有逐层抽压法和真空袋法,这都是早期做法,现多为真空室抽压法(见图7-5-1)。
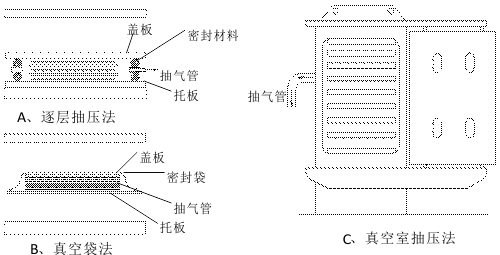
图7-5-1 抽压法示意图
(1)逐层抽压法
将托板及盖板加大,在叠合后,在托板与盖板之间放入耐热有弹性密封材料(留有抽气口),将其送入压机以后边对其抽真空,同时升温升压进行层压(见图7-5-1 A)。
(2)真空袋法
将每一叠合套上耐热耐压袋(留有抽气口),然后将其推入压机中,对其抽真空同进升温升压进行层压(见图7-5-1 B)。采用真空袋法优点是原来工模具都不用改变,操作过程比较简单。
(3)真空室抽压法
由于上述两种操作都比较繁琐,所以出现了将整台压机四周密闭,留门作进出物料及设备维修用的真空压机。门有上开式、下开式,也有侧开式。这种压机结构比较简单,操作比较方便,因而得到广泛应用(见图7-5-1 C)。
2.舱压法
产品层压是在一个大型圆柱体型卧式大钢罐中进行,卧式钢罐称为压力舱(见图7-5-2舱压法示意图),留有进出物料的门。待压的“叠合”安放在一块装有抽气管的承载盘上,用一块粗厚的毯状织物先将叠好的“叠合”覆盖住,再用不透气、耐热的塑胶袋套在其外面并将其密封,留有抽气口。将装有“叠合”的承载盘推入压力舱,可以同时推入由不同尺寸,不同规格材料组成的“叠合”。将压力舱门密闭后,在对承载盘进行抽真空同时,也往压力舱中通入高温高压二氧化碳或氮气(作为加热介质,也是压力介质),对待压制品进行热压。压力舱内设有循环风扇,以使舱内各处温度均匀。
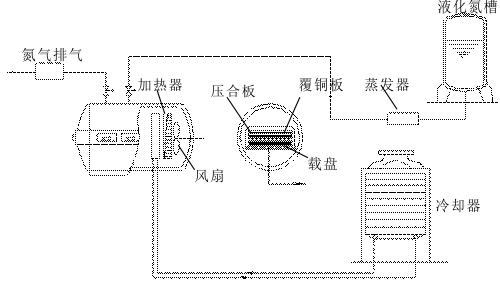
图7-5-2之A、舱压法装置示意图
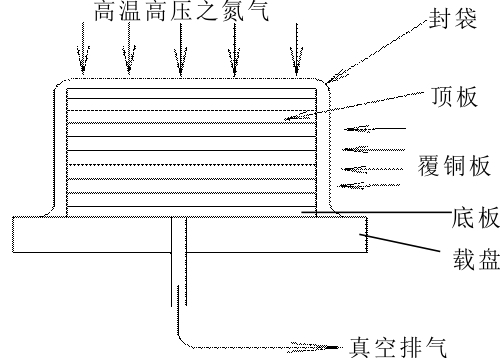
图7-5-2之B、舱压法气压压合示意图
舱压法与层压机最大区别:层压机是采用垂直上/下机械挤压式,而舱压法压力则来自气体。
舱压法最大优点:由于压力是来自气体,各个方向压力都是相等的,因而不会出现机械压力上/下挤压式所出现产品四周流胶较多,而导致产品中间厚四周薄,产品存在内应力而翘曲度较大等问题;采用舱压法可以同时压制各种不同尺寸,不同规格型号产品,包括一些特殊结构产品,由于舱压法不会存在白边角问题,产品空隙少,尺寸稳定性好,可以缩小毛坯尺寸,节省原材料,因而在某些特殊领域,舱压法具有优势。
舱压法主要缺陷:以气体对流传热,传热过程慢,热效率低,生产周期长,生产效率较低。
(二)层压机加热方式
覆铜板层压机加热方式主要有蒸汽、过热水、热媒油三种方式。
1.蒸汽加热
由蒸汽锅炉直接将蒸汽送到层压机。蒸汽的温度是与蒸汽压力成正比的,只要控制好蒸汽压力,就达到控制温度的目的。以蒸汽作为热源,层压机温差波动较大。热压板冷却降温可以用冷水直接进行冷却。以蒸汽加热设备构成比较简单,投资较少,因此仍被不少覆铜板厂采用。
2.过热水加热
由蒸汽锅炉给过热水贮罐加热,当温度达到设定值以后,蒸汽锅炉只是补充过热水贮罐热损耗,因此,采用此种设计比较节能。过热水贮罐和层压机有一个迴(回)路,当层压机需要加热时,由泵将贮罐内过热水泵入层压机热压板中。热压板本身又有一个热循环,当因热量损耗达不到设定要求时,贮罐会补入一些新鲜过热水,以保证热压板温度保持在工艺要求范围内。因此温差可以达到±1℃范围内。降温时则将层压机迴路过热水通过一个热交换器使热水逐步降温来实现。也可以单独一条冷却水迴路来完成热压板冷却降温。采用过热水相对投资较大,在国内覆铜板厂未见有应用报导,国外覆铜板厂用的较多。
3.热媒油加热
热媒油加热形式和过热水相似,也是通过一个热媒油贮罐来实现的。热媒油锅炉给热媒油贮罐供热。热媒油贮罐给层压机加热。热压板本身又有一个热循环,当热压板温度低于设定值时,热贮罐会补入一些新鲜的热媒油以维持热压板温度在设定范围内,通常温差可以控制在±1℃范围内,满足覆铜板生产要求。降温是将热压板热油循环经过一个或若干个热交换器,使热油逐步降温来实现热压板逐步降温目的。由于降温过程对产品翘曲度、尺寸稳定性有一定影响,所以层压机降温有多种形式设计,它既要适应工艺要求的先慢后快降温的要求,以保证产品质量,又不会使生产周期太长,同时要有利于节能。用过热水加热,与蒸汽一样,过热水的温度也是与压力成正比,因此系统压力较高,危险性很大。热媒油加热则是常压,系统压力是输送热媒油泵压力,不会有什么危险性,热媒油系统造价也较高。由于其温度控制精度较高,如果生产中需要更高供热温度时也能实现,因为合成热煤油热分解温度在310℃以上,而蒸汽和过热水是达不到的,而且国内已有不少覆铜板厂采用媒油加热系统。
采用过热水与热媒油作为层压机热源时,要仔细计算层压机热能需求,以确定热媒油锅炉供热能力及热媒油贮罐体积。设计时,应预留工厂发展空间。
(三)连续铜箔发热层压机
蒸汽、过热水、热媒油加热都是先将热压板加热,再由热压板将热量透过托板、垫板材料、不锈钢板逐张传给压制产品,热量从最外边一块板传到最中间一块板有一个时间差。先受热的粘结片固化过程比后受热粘结片固化过程要早若干时间,这个时间差与每一叠合产品厚度及层压产品张数相关,不管层压工艺上怎么改变都无法选择到一个既适合最外层产品,也适合最内层产品的层压工艺,造成热压时,每一叠合中产品张数受到一定限制。
连续铜箔发热技术是针对上述加热法缺陷的一种改进。其作法是配箔组料时,不是用片状铜箔,而是用连续铜箔,即每张板铜箔是首尾相连(见图7-5-3)。将最上表面及下表面铜箔连接到整流器上。当由整流器输入大电流时,则所有铜箔面就产生大量热量,使每块产品同时受到同样热量,因而可以使每块产品固化进程相同,可以找到一个最佳上压时间,提高产品质量,减少能耗,也免除了层压机上热压板,可以降低层压机制造费用。此种装置组料是在一个特殊叠片机上完成的,这种装置已有人将它用在PCB厂多层板压制中。待以时日,覆铜板叠料叠合的某些难题如能及时很好解决的话,也有可能在覆铜板行业中广泛使用。
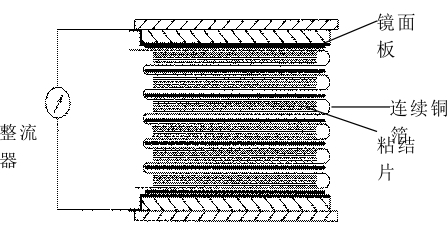
图7-5-3 连续铜箔层压示意图
(四)热压板结构
热压板是层压机核心,也有人将它称为热盘。它的加工精度及温度精度对产品性能影响极大。加工精度指热压板的平行度、平坦度,其加工精度与产品厚度偏差相关联。热压板内管路结构与传热效果,温度精度相关。较常用的管路结构有单管式与双管式,单进单出式和双进双出式。单管式指管路在横向是单管相连。双管式是指管路在横向是双管相连,双管式加工难度较大。单进单出式管路多数从热板一个角为入口,对角为出口。这种结构由于管路路程较长,入口和出口有较大温差,压制产品易产生扭曲。单进单出式管路入出口也有在中间入、中间出。这种结构入、出口温差相应较小,管路加工比对角进出稍难一些。为了更好消除入、出口温差以及热压板四周因热量散失大于中部状况,所以有双进双出式。这种结构管路在热压板两边有两个入口,在中间有两个出口。由于运行中总有热损耗,所以入口温度高于出口温度。采用这种结构与提高热压板外围温度目的一致。必要时,在管径设计上,也应以热压板周边管径略大于中间部位管径。或热压板管路密度周边部位略大于中间部位。双排管结构形式,也是基于更好消除热压板温差,提高四周部位供热效果而设计的一种管路结构。
(五)进出料结构
层压机进出料一般都采用推拉式。为了使在推拉过程中不因急停车而造成板件错位,影响到压制质量,也避免急拉急停而造成铜箔表面损伤。因此推拉机构应该采用慢—快—慢运行方式。长期推拉,必定造成热压板表面磨损。为了减少热压板修磨(热压板面积大,加工精度高,一般工厂不具修磨热压板技术条件),通常在热压板表面加上一张厚度精度较高的薄不锈钢板作为保护板,盖在热压板表面,以延长热压板寿命。
为了避免热压板表面被磨伤,有些设备厂家将进出料机构设计成提/放式,入料时,采用提—推—放动作。出料时,采用提—拉—放动作。由于在推拉前、后“叠合”均已被提升起来,到达位置后再放下,在推拉过程就不会接触到热压板,因而就不存在磨损热压板的问题。此种取送方式还可以保证镜面板与铜箔不产生错动,对提高层压质量有利。
二、层压机装置
覆铜板层压生产中有采用热/冷一体机(层压过程升温升压,保温保压,降温冷却在同一台压机上完成),也有采用热、冷分体机,即层压机始终保持热态,产品降温冷却过程由冷压机完成。
(一)热/冷一体层压机
热/冷一体层压机是将已叠好的叠合全部送入压机以后,才开始升温升压,保温保压,降温冷却。当产品降至50℃以后,才将“叠合”全部从压机中拉出来,送至分板线分板。这一作法缺点是热压板由冷变热,再由热变冷,能源消耗太大,生产周期长,设备利用率较低。但当前仍有不少覆铜板厂采用热/冷一体机。特别是在对覆铜板尺寸稳定性及减少翘曲度问题上,不少覆铜板厂认为热/冷一体机升降温过程比较缓和,有利于提高产品尺寸稳定性及平整度。对于一些超薄型覆铜板生产更多地使用热/冷一体机。
(二)2热1冷层压机系统
采用热冷分体机最大特点是节省能源,减少热压板升、降温过程中不必要的能量消耗,设备利用率也提高。因而被不少覆铜板厂所采用。最常用配合为2热+1冷系统(见图7-5-4)。这一系统由2台层压机、1台冷压机、1台入料贮料架、1台出料贮料架和1台入/出料移动台车组成。(也有采用固定入/出料机、移动台车不带入/出料机,只是来回运送物料)。其操作过程:入料架装满“叠合”后,由移动台车将其转移到层压机。层压机始终保持摄氏一百多度状态。“叠合”进入层压机以后经历升温升压——保温保压——降温(降压或不降压)周期。但降温不会降至100℃以下,使层压机始终保持热态。当这一周期进行完了以后,由移动台车将物料转移到冷压机继续加压,降温,待产品温度降至50℃以下时,将其由冷压机转移至出料架,再转送至分板台分板。产品送至切板验板线,不锈钢镜面板(经或不经过水洗机)回流至叠合线,托板直接回流至叠合台。
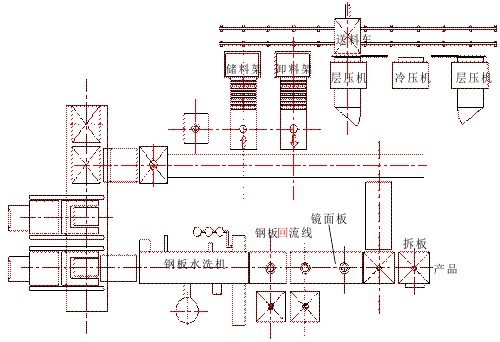
图7-5-4 2热1冷层压叠合配置示意图
(三)不锈钢板水洗机与不锈钢板研磨机
不锈钢板水洗机由上、下各一付或各两付磨刷与水洗段,风干段组成。磨头有感应式(可自动调节与钢板接触压力)及固定式(由电流表或其它形式仪表反映磨刷与钢板接触压力,由人工调整磨刷与钢板接触面,以获得满意磨刷效果)。磨刷除了连续转动外,还会同时沿轴向来回串动,以增加磨刷效果。为避免磨刷下来的杂质会随循环水到镜面板表面,挤、擦伤镜面板,所以循环水应过滤使用。风干段可以用热风刀,也可以只用冷风刀。只用冷风刀可以节省能源。但务必使从水洗机出来的镜面板表面没有水气。
由于不锈钢板水洗机价格比较昂贵,而在正常生产过程中,如果产品的A级品率能稳定在90%以上,则不锈钢板表面可能存在的灰尘杂质是很少的,只要在生产线上加强检查并用人工及时予以局部清理(如用600目或800目水磨砂纸擦去钢板上局部杂质),同时配置一台不锈钢板研磨机,对一些表面有伤痕及粘附在表面不易清理的不锈钢板进行研磨抛光,再返回到生产线中去,也可以达到良好效果。因此,国内有不少覆铜板厂回流线中没有配置不锈钢板清洗机。
不锈钢板研磨机结构如图7-5-5所示。它由砂带、压紧轴、张紧轴、工作台面、传送带等部分构成。它根据设备可装砂带数量分单轴、双轴。单轴指只能装一条砂带。双轴则一次可装二条砂带,提高研磨效果。通常使用单轴研磨机已可以达到使用要求,所以在覆铜板厂中,选用单轴研磨机比较多。工作台面可以升降,当接触压力大时,磨削阻力大,电流量则加大。接触压力小时电流显示也就小。操作者根据操作经验选择一合适电流量作为调节工作台面升降程度依据。此种调节方式研磨结构比较简单,但已可满足生产工艺要求。也有一种全自动感压装置,当砂带和不锈钢板接触压力不在设定值范围时,会自动调节工作台面升降,以保持砂带对不锈钢板压力恒定。但设备自动化程度越高,设备造价越高。选用设备时,以能否达到工艺要求作为评估参考。砂带除了与不锈钢板运行方向相反方向高速转动外,还沿着压紧轴方向来回串动,以提高研磨抛光效果。不锈钢板研磨机要配备多种型号砂带,最粗的可以选用到80目,最细的选用600目也足够了。根据实际研磨效果及时对不锈钢镜面板研磨等级要求制定相应的研磨工艺。不锈钢镜面板研磨,应顺原钢板纹路研磨,以保持原钢板晶态,以提高研磨效果,延长使用寿命。
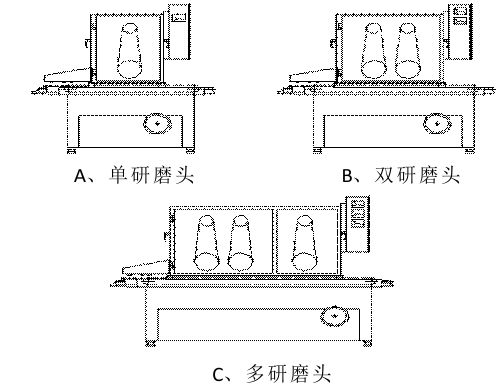
图7-5-5 不锈钢板研磨机示意图
在全自动叠合线中,配置不锈钢板水洗机,对于稳定产品外观质量是有帮助的,有条件的工厂应尽量配置。
(四)不锈钢板与托板
不锈钢板是覆铜板生产中必不可少的工装模具,不锈钢板质量与覆铜板质量息息相关。不锈钢板如同一面镜子,它上面有什么样的缺陷,那么压制出的覆铜板也就有什么样的缺陷。因此,选用和正确使用维护保养好不锈钢板是覆铜板生产和质量管理中重要的一环。不锈钢板选用有材质、硬度和加工精度要求,因为不锈钢板常见的缺陷,如砂眼、孔隙、锈点与不锈钢板材质与加工方法有关。在不锈钢板使用一段时间后,进行修磨时,质量不好的不锈钢板磨去表面层后就会出现砂眼、孔隙等缺陷。它会影响产品质量和直接造成不锈钢板报废。锈点经常出现在经水洗而长期没有使用的不锈钢板。因此,使用者要改变不锈钢板不会生锈的观念。对于环氧玻纤布基不锈钢板来说,由于对产品外观质量有较高要求,所以希望不锈钢板有较高硬度及较高的表面硬度,以减少不锈钢板表面出现伤痕、凹坑等缺陷的产生。在生产环境净化程度比较高,又采用全自动叠合线操作的条件下,不锈钢板受损伤机会很少。有些覆铜板厂也逐步试用一些硬度稍低的不锈钢板,以减少投资。
不锈钢板加工精度主要为平行度、平坦度及光洁度。不锈钢板的平行度、平坦度至少应与热压板同一等级或略高于热压板,才能保持产品的厚度偏差达到预定技术范围。不锈钢板表面光洁度通常用研磨抛光砂带型号相对应符号表示,如No.4或No.6,表示以400目或600目砂带抛光。如果有进一步要求,则应以粗糙度等级表示。由于达到No.4或No.6时,不锈钢板表面已很光亮,有如镜子一样可以照人,所以覆铜板生产所用不锈钢板也常称为不锈钢镜面板,或直接称为镜面板。不锈钢板厚度要配合生产要求进行合理选用,以产品质量保证为前提,同时也要考虑有利于生产效率的提高。目前,各厂家选用的厚度一般为1.5~2.2mm。
托板在长期生产中容易产生变形而严重影响产品质量。因此,托板质量除了其平行度、平坦度技术指标应与不锈钢板相同之外,应尽量采用高强度钢材以及较厚厚度,以防止其在生产中产生变形。层压机台面越大,则应选用厚度更厚的托板。通常托板厚度以6~10mm为宜。在生产中,必要时,要定期将托板翻转使用。托板应磨去棱角,以免划伤不锈钢板。
三、环氧玻纤布覆铜板压制成型技术
环氧玻纤布覆铜板压制成型技术与产品质量密切相关,比较突出的如产品翘曲度、白边角、光凹、厚度偏差、尺寸稳定性、Tg值等均与层压条件设定情况有关。层压成型技术是覆铜板生产三大技术要素(树脂配方、上胶技术、层压成型技术)中的一个。根据选定树脂配方及粘结片技术指标,设定层压条件,是提高成型产品质量,提高生产率的一个重要措施。
(一)非真空层压机覆铜板压制成型技术
非真空层压机没有真空室,压制成型过程可以观察到粘结片流胶及凝胶转化过程,所以比较容易判断最佳加压时间。环氧玻纤布覆铜板压制成型可以采用一次加压,也可以采用分段加压,一次加压与分段加压各有优缺点,应视树脂配方与粘结片技术指标而定。一次加压与分段加压如图7-5-6所示。
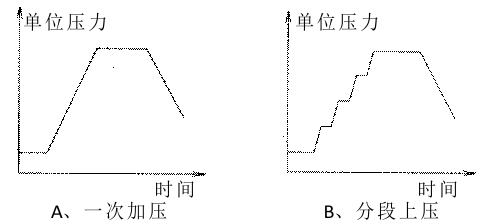
图7-5-6 覆铜板层压压力分配示意图
对于非真空非自动控制层压机,产品最初压制成型时,可采用边升温边逐步升压,观察流胶与凝胶化过程来确定层压条件。通常,都先给一个起始压力(俗称接触压,压力在每平方厘米数公斤到十几公斤范围)。然后,依据双氰胺固化历程与温度关系及累积操作经验,初步确定几个升温段和压力段。当粘结片开始软化,熔融树脂开始渗出之时,应逐步跟紧压力,以让铜箔紧密贴合粘结片及赶走粘结片上气体。随时观察粘结片上被挤出胶的凝胶化过程,可以用竹签或铁丝从粘结片上挤出的胶上挑一小块下来,在层压机边上搅动试拉丝情况。当接近可拉丝时及时将压力打到工艺设定最高段压力(不可等到拉断丝才上高压,上压太迟基板会出现白斑与干花)。作胶团拉丝情况时,应同时作每一叠合最外层产品及最中间产品。最外层产品拉丝早,中间产品拉丝晚。以升温速度来协调,使最外层及中间部位拉丝时间尽量接近。加最高压时间应以最外层板拉丝状况为判定依据。以免加压迟了最外层产品起白斑或产生干花。如果层压产品性能合乎技术指标时,以这一试验进程编制非真空层压条件。
热压条件分升温升压,保温保压,降温三个大部分组成。对于FR-4型覆铜板,保温温度(产品温度)不宜低于170℃,以免产品固化不充分。但保温温度也不宜高于180℃,以免产品颜色变深,性能下降。保温时间不宜低于60分钟,保温时间太短同样有固化不充分问题。保温时间太长则有生产率低问题。产品降温到50℃以下,使产品完全冷却定型。降温过程不宜过急,以免产品产生内应力而翘曲变形及影响产品尺寸稳定性。
(二)真空层压机覆铜板压制成型技术
真空层压机由于有真空室,层压过程观察不到制品流胶与凝胶化过程。因而层压条件设定依据双氰胺固化历程与温度关系及累积操作经验设定。同样可以有一次加压及分段加压二种工艺路线。所谓一次加压,是在将叠合放入压机,给予接触压之后,视升温与粘结片凝胶化进程而一次将压力加到最高设定值。而分段加压,是在接触压之后,视升温与粘结片凝胶化进程分多次加压。采用何种工艺路线应视树脂配方、粘结片技术指标而定。不管是一次加压还是分段加压,最关键要使升温段、升温速率与加压时机密切配合,才能达到最佳效果。在设定层压条件时,应结合每一叠合产品张数来设定升温速率与加压最佳时机。产品在层压机中的传温过程是有一个梯度,每张产品传热都滞后一定时间(见图7-5-7)。随着每一叠合产品张数增多,最中间一张产品要到达与最外层一张产品相同温度时间差就越长。如果升温与加压时机掌握不够准确,就会出现最外层产品合适,中间产品流胶太多,或中间产品合适,最外层产品起白斑,出现干花等质量问题及白边角偏大等问题。当今真空层压机压制FR-4型覆铜板,每一叠合产品张数少的有10张,多的可达20张。由于层压成型工艺技术与产品质量及生产效率密切相关。在本书中,笔者已对主要工艺路线,工艺参数作了论述,只要循这条路作下去,就能找到适合自己工厂的生产工艺条件。
由于真空层压机能将粘结片中气体及层压过程中产生的水份与低分子物及时排出,使压制产品有较高密度。因而单位成型压力可比非真空压力低一半或一半以上。当真空度达到95%以上时,FR-4型覆铜板单位成型压力在20~30Kg/cm2就可使产品达到良好压制效果。
覆铜板压制成型时垫板材料起着热量和压力的缓冲作用,以使叠合中的每张产品都能均匀地受热受压。通常,随着每一叠合产品张数增多,应适当增加垫板材料数量或厚度,以保证最外层产品质量与内层产品质量一致性,减少内层产品白边角及外层产品翘曲度。因此,垫板材料材质,厚度对层压效果有很大影响。当前较常用的为牛皮纸,其标重从80g/m2~240 g/m2甚至更厚。重要的是牛皮纸的厚度均匀性要好,吸水率要低,以防层压过程中牛皮纸结成块。使用过程中牛皮纸力保干燥,才能提高使用效果。至于每叠垫板纸数量视所使用牛皮纸标重与每一叠合产品张数灵活运用。通常每张牛皮纸可使用2~3次。也有一些覆铜板厂使用一种由耐热毡状物作为垫板材料。此种耐热毡状物含有耐热纤维,石棉或耐热橡胶等成分,具有适当的热传导性,可经多次反复使用。采用这种整块垫板材料,可以简化操作。
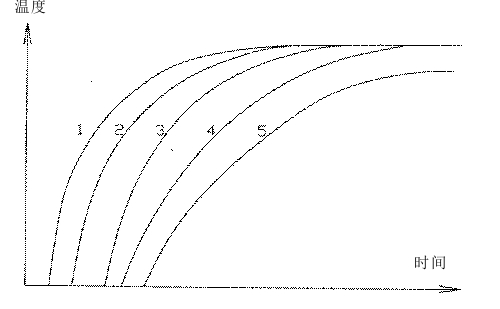
图7-5-7 覆铜板层压过程产品温度分布示意图 但是,这种整块垫板材料,在使用一段时间后,因受热老化及长期高压作用,其密度会逐渐变大,对热量、压力的缓冲作用逐渐下降。 |
|
|
|
|
|
|
热点新闻 |
|
|
|