|
当前位置:首页>网上讲座>第七章 第八节 环氧玻纤布覆铜板技术新进展 |
|
|
第七章 第八节 环氧玻纤布覆铜板技术新进展 |
|
|
|
随着电子信息产业的迅速发展,电子产品和电路组装技术上了一个新台阶,它促使印制电路板制造技术向微孔径、细线条、高密度布线及高多层方向发展。基板的耐热性、低膨胀系数、高尺寸稳定性、低介质损耗等要求,就摆到了覆铜板工作者面前。普通的FR-4型覆铜板已经满足不了更高性能要求的PCB制作。新产品开发是势在必行。而且,随着环境保护呼声日益提高,开发、生产环保型覆铜板也摆到议事日程上来。
下面从产品特性方面论述环氧玻纤布覆铜板技术动向与进展。
一、FR-4型产品高性能化
由于FR-4型覆铜板具有覆铜板生产工艺性能好,PCB制程工艺性能好,产品综合性能优良,成本低廉等优点,而成为PCB行业中用量最大的一类覆铜板。虽然随着印制电路向精细线路、薄型高多层方向发展时,FR-4型覆铜板的某些性能已不能完全满足PCB制作要求。但只要在FR-4型产品基础上,通过某些改性措施,如采用本文所提及的併用环氧树脂技术或併用固化剂技术,或对树脂进行接技、嵌段、共聚合等方式加以改性,来提高产品某个方面的性能。使之符合PCB制作中某些方面技术要求。下面我们就比较突出的几个产品论述之。
1.高Tg覆铜板
环氧树脂固化体系是非晶态结构,它有如下三种物理状态:玻璃态,高弹态和粘流态。玻璃态下,高分子物分子不能内旋转,分子链段也不能移动和平移,分子只能在平衡位置上振动;随温度升高,高聚物外观变得柔软和富有弹性,高聚物此时状态称为高弹态;随着温度继续升高,其整个分子链都可以运动,此时高聚物在外力作用下可以流动,此种状态高聚物称为粘流态。高聚物由玻璃态向高弹态转化温度称为玻璃化温度(Tg)。
由于高聚物在玻璃化温度以下时,其外观是硬质固态,具有机械强度。因而,提高Tg就提高了产品的使用温度。当前FR-4型覆铜板Tg值在130~140℃间。而PCB制程中有好几个工序超过此温度范围,虽然加工过程在Tg以上所处时间较短,当加工温度在Tg以上时,固化物体系分子运动状态开始发生转变,并对制品的加工效果及制品最终状态(如翘曲、尺寸稳定性等)会有一定影响。因而,提高Tg值,使覆铜板在PCB制程中保持其基本特性,是当前提高FR-4型覆铜板耐热性的一个主要方向。提高FR-4型覆铜板Tg值的一个重要手段是提高固化体系的交联密度或在树脂配方中增加芳香基的含量。在新产品开发时,视所要达到Tg值目的而采用其中一种方法。也可以两种方法同时并用,如在FR-4型树脂配方中增加多官能环氧树脂或线性酚醛环氧树脂,以提高固化体系的交联密度,达到提高Tg目的。也可采用含芳香核固化剂,增加固化体系芳香基含量,也可达到提高基板耐热性目的。当要达到更高Tg值时,则可考虑两者并用。根据PCB制程及用户需求,较常用做产品目标Tg值有Tg=150℃、Tg=170℃、Tg≥180℃、Tg≥200℃等。由于以FR-4型覆铜板进行改性而形成一系列高Tg产品,既保留了FR-4型覆铜板优良的综合性能,又具有在覆铜板生产工艺过程,PCB生产工艺过程均不须改变,成本相对一些特殊性能覆铜板低廉等优点,而得到迅速发展。
2.UV阻挡型覆铜板
进入90年代以后,在PCB制造工艺中普遍采用涂覆液态感光阻焊油墨(俗称湿菲菻)代替网印热固型阻焊油墨进行图形阻焊保护技术,并采用紫外光(UV光)对基板双面同时曝光进行显影固化。当采用通常环氧玻纤维布基覆铜板时,由于UV光能穿透基板,那么当PCB制程中双面同时曝光时,每一面的UV光都会穿透基板到达另一个面。在每个面都涂有感光阻焊油墨时,每个面的感光图形都会投射到另一个面上去,形成感光“重影”,严重影响了阻焊图形质量。因此,对于以UV光固化阻焊油墨工艺基板必须具备阻挡UV光穿透性能。
阻挡UV光透过的方法很多,由于基板是由玻纤布和环氧树脂两种材料构成的,对这两种材料中的每一种进行改性或两种材料同时改性都可以达到阻挡UV光透过的目的。
如对玻纤布进行改性,通常覆铜板所用E-玻纤布是不具阻挡UV光性能,但可以在E-玻纤配方中加入具有阻挡UV光的组份,如加入1.9~6.0%重量分的Fe2O3和0.2~6.0%重量分的TiO2,由此生产的玻纤布对波长360μm的紫外光透过率为0.0~0.2%,且对波长420μm的紫外光透过率也在8%以下,用此种玻纤布与环氧树脂制成覆铜板,就具有足够阻挡UV光穿透性能,也可以对玻纤拉丝用的浸润剂进行改性,如在浸润剂中加入阻挡紫外光的TiO2荧光增白剂和紫外光聚合引发剂(常用荧光增白剂有芪类和苯并咪唑类,常用紫外光聚合引发剂有双低烷基氨基苯酰苯),它们可以单独使用,也可以併用。这种浸润剂需制成玻纤布织造完成后不需进行“脱蜡”处理,因此,此种浸润剂可采用改性环氧树脂做成膜剂,再加入硅烷偶联剂和表面活性剂等。由该法制成玻纤布具有很高的阻挡UV光性能;也可以在普通E-玻纤布表面被覆具有阻挡UV光的TiO2粉,荧光增白剂和紫外光聚合引发剂等,都可以使由其和环氧树脂制成基板具有阻挡UV光性能。上面所述的是玻纤布阻挡UV光的一些作法,其能否大量用于阻挡UV光基板生产,应由玻纤布制造厂和覆铜板厂去选择。
在环氧树脂中添加阻挡UV光的组分是可以采用又一种方法,它可以在环氧树脂中添加阻挡UV光的TiO2粉或加入荧光增白剂和紫外光聚合引发剂。也可以在环氧树脂中添加具有阻挡UV光功能的另一类环氧树脂,这种方法在FR-4型覆铜板生产中被大量采用,而,这种方法的被采用,还带有一些巧合性。因为试验中科研人员是意图提高覆铜板耐热性,在溴化双酚A型环氧树脂中添加四官能环氧树脂,其化学结构为:
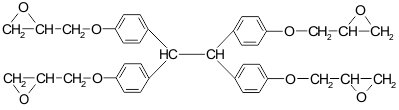
化学名称:1.1.2.2-四羟基苯乙烷四缩水甘油醚。
由于采用四官能环氧树脂可增加固化体系芳核含量及提高交联密度,因而用其制取覆铜板(俗称“黄板”)可以有更高Tg值。而当这种产品在PCB应用中,人们发现它具有优良阻挡UV光性能,而且具有荧光特性,适合PCB生产中AOI自动光学检测。1993年以后具有阻挡UV光FR-4型覆铜板(黄板)正式进入市场,1995年以后我国也开始用四官能环氧树脂生产阻挡UV光黄板。
阻挡UV光FR-4型覆铜板中,四官能环氧加入量视用户对产品的性能要求而定。如果以提高Tg为主要目的,那么加入量可以为基本环氧树脂量的6~10%(重量比)比较适宜。如果以阻挡UV光为目的,在PCB加工中紫外光曝光机波长约在365纳米,溴化双酚A型环氧树脂不具阻挡UV光功能。但主要混入适量四官能环氧树脂到具有很好阻挡UV光功能(见图7-8-1)。
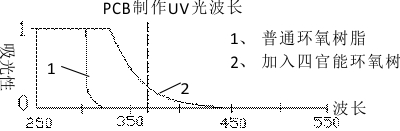
图7-8-1 四官能环氧树脂阻UV光功能
对于PCB生产中自动检测AOI系统,需有黄光。四官能环氧树脂在442纳米黄色激光照射会发出荧光并可在550纳米波段测量。要达到阻挡UV光和满足自动光学检测AOI系统要求,四官能环氧树脂加入量可在4~10%范围选用。
如果原来FR-4覆铜板是以2-MI为促进剂,在添加了四官能环氧树脂以后,仍要保持原来流动度,由于2-MI和四官能环氧树脂在流动度变化上有如下关系(见图7-8-2)
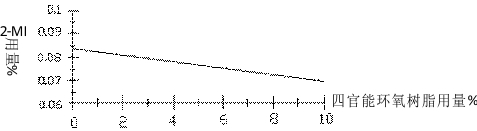
图7-8-2 流动度一定时,2-MI与四官能环氧树脂用量关系图
由上图可见,要保持原流动度,增加四官能环氧树脂量时,可适当减少2-MI用量。
3.满足无铅化要求的覆铜板
2003年2月13号,欧盟颁布了RoHS和WEEE两大指令,要求“2006年7月1日起,新投放市场的电气电子产品不得含有:铅、汞、镉、六价铬、多溴联苯(PBB)和多溴二苯醚(PBDE)等6种有毒物质 ”。
该指令的颁布和实施标志着全球电子业无铅化时代已经来临。
无铅焊接和有铅焊接工艺的差别如表7-8-1所示。
表7-8-1
|
Sn63/Pb37 |
SAC305 |
无铅焊接和有铅焊接工艺的差别 |
1 、熔点 |
183 ℃ |
217 ℃ |
熔点高34℃,焊接温度提高:在回流焊方面最少高25℃,在波峰焊方面最少高20℃ |
2 、液态经历时间 |
60 秒 |
90 秒 |
无铅焊在高温下经历的时间长 |
3 、蘸锡时间 |
2 秒 |
6 秒 |
无铅焊接行程缓慢 |
4 、焊后的降温速度 |
3 ℃ /S |
6 ℃ /S |
无铅焊接降温速率快 |
由于无铅焊料要求更高的预热温度,更高的焊接温度和更长的高温焊接时间,因此PCB基板将受到比传统Sn-Pb焊料体系更大的热冲击和热应力,从而使PCB基板带来更大的损害,主要体现在五个方面:
(1)、基板分层,变色
(2)、导通孔裂缝,断开等
(3)、焊盘(连接盘)翘起、脱落
(4)、PCB板翘曲变形
(5)、更易发生CAF现象
美国IPC标准率先提出“无铅”FR-4产品标准,在FR-4板材标准的基础上,对无铅化基材增加热分解温度(Td)、耐热分层时间(T260/T288/T300)及Z-轴热膨胀系数(CTE)等三项耐热性要求,如表7-8-2所示。
表7-8-2 IPC4101C标准耐热性要求
IPC-4101C标准 |
Tg |
Td(℃) |
T260(min) |
T288(min ) |
T300(min) |
Z-CTE(%) |
IPC-4101C/99 |
含填料,Tg>150℃ |
≥ 325 |
≥ 30 |
≥ 5 |
- |
≤ 3.5 |
IPC-4101C/101 |
含填料,Tg>110℃ |
≥ 310 |
≥ 30 |
≥ 5 |
- |
≤ 4.0 |
IPC-4101C/102 |
含填料,Tg>185℃ |
≥ 340 |
≥ 30 |
≥ 15 |
2 |
≤ 2.8 |
IPC-4101C/103 |
含填料,Tg>150℃ |
≥ 325 |
≥ 30 |
≥ 5 |
- |
≤ 3.5 |
IPC-4101C/121 |
无填料,Tg>110℃ |
≥ 310 |
≥ 30 |
≥ 5 |
- |
≤ 4.0 |
IPC-4101C/122 |
无填料,Tg>110℃ |
≥ 310 |
≥ 30 |
≥ 5 |
- |
≤ 4.0 |
IPC-4101C/124 |
无填料,Tg>150℃ |
≥ 325 |
≥ 30 |
≥ 5 |
- |
≤ 3.5 |
IPC-4101C/125 |
无填料,Tg>150℃ |
≥ 325 |
≥ 30 |
≥ 5 |
- |
≤ 3.5 |
IPC-4101C/126 |
含填料,Tg>170℃ |
≥ 340 |
≥ 30 |
≥ 15 |
≥ 2 |
≤ 3.0 |
IPC-4101C/127 |
含填料,Tg>110℃ |
≥ 310 |
≥ 30 |
≥ 5 |
- |
≤ 4.0 |
IPC-4101C/128 |
含填料,Tg>150℃ |
≥ 325 |
≥ 30 |
≥ 5 |
- |
≤ 3.5 |
IPC-4101C/129 |
无填料,Tg>170℃ |
≥ 340 |
≥ 30 |
≥ 15 |
≥ 2 |
≤ 3.0 |
IPC-4101C/130 |
含填料,Tg>170℃ |
≥ 340 |
≥ 30 |
≥ 15 |
≥ 2 |
≤ 3.0 |
IPC-4101C/131 |
无填料,Tg>170℃ |
≥ 340 |
≥ 30 |
≥ 15 |
≥ 2 |
≤ 3.5 |
以DICY为单一固化剂的覆铜板,其耐热性往往达不到无铅化产品的耐热性要求,为了达到以上几项耐热性的要求,需要开发新的胶液配方。一般是以酚醛树脂代替DICY作为环氧树脂主要的固化剂,同时为了降低Z-轴热膨胀系数,需要使用一定比例的无机填料,无机填料的比例越多,Z-轴热膨胀系数越小,一般无机填料的比例控制在5-25%。关于无机填料的使用,在第九节有专门的论述。
4.耐CAF覆铜板
导线间距离的缩短,使得导体间的单位距离电压也随之提升,导体(如金属化孔或线路)中金属离子受直流电场的影响下,产生电化学反应,金属被溶解成离子,并在导体之间的绝缘层(或表面)有析出的现象。在高温湿环境、施加电压条件下,来自导线电路或金属化孔上的铜金属离子由电极析出,产生迁移。沿着玻璃纤维上的铜离子迁移而发生的电蚀现象,称为导电阳极丝(Copdutive Anodic Filament, CAF),CAF的发生,将使导体间的绝缘电阻下降,以至发生短路,它严重影响PCB的可靠性。
覆铜板CAF的测试条件一般为:温度85℃、湿度85%、电压50VDC,测试时间至1000小时,静态测试时测试点之间的电阻小于108欧姆即判断失效。
大量研究表明,板材的CAF主要与下列因素有关:胶液配方的固化体系、树脂与玻纤布表面的亲合性、孔洞、杂质、吸水率、导线间距、孔粗糙性等。因此改善上述要素将有助于提高覆铜板材的耐离子迁移性。从产生的原因看,影响板材CAF特性的因素是综合的,既有基材自身特性的问题,也有PCB加工制作的原因,因而,必须进行综合治理。
(1)胶液配方的固化体系:DICY和PN是环氧树脂的两种最常见的固化剂,一般情况下,DICY做固化剂的板材其CAF性能相对较差,而PN做固化剂的板材其CAF性能相对较好,这与DICY容易吸水有关。不过采用DICY做为主要固化剂的板材,通过采用其它相关技术,也可以大幅度提高板材的耐CAF性能。
(2)采用新型的玻纤布:采取新型玻纤布,提高树脂对玻纤布的浸润性,使树脂与玻纤布的粘合更牢固。如通过对玻璃纤维的开纤,而使纤维膨松,使丝与丝之间、纱与纱之间、结点与结点之间的显微空间增加,同时降低纱与纱之间的表面张力,使偶联剂更易润湿丝和纱的表面,从而使浸涂树脂时使其能充分与丝和纱的表面结合,提高树脂对玻纤布的浸润性,减少板内的显微裂纹和显微气泡,使板内的尤其是沿纱表面分布的“空穴”数量减少,从而提高耐离子迁移的能力;另外,玻纤布偶联剂的合理选用,将大大提高玻纤与树脂的结合力。
(3)减少树脂中离子的含量:板材中多种离子的存在,对铜金属离子迁移起着促进作用,从产生CAF的部位的分析表明,该位置聚集的离子除铜金属离子外,氨离子与氯离子成为最主要的成分,氨离子主要来自于环氧树脂的固化剂——— 双氰胺,而氯离子则源于树脂合成时,残留在树脂中的可水解氯,提高板材的耐离子迁移性,就得要尽量降低氯离子与氨离子的含量。
(4)降低板材的吸水率:板材中的水分是产生离子迁移的根源,没有水的存在,离子便不能移动,迁移现象也将不存在,因而,减少板材的吸水率,将有助提高耐离子迁移性。
(5)提高线路板金属孔的质量:选择合理的加工参数,使孔壁光滑,无毛刺,避免玻纤与树脂间有微裂痕产生,从而杜绝CAF产生所需的通道。 5.高CTI覆铜板
CTI中文名:相比漏电起痕指数,英文名:Comparative Tracking Index。
绝缘基材的表面受到尘埃附着、水份结露或潮气和具有正负离子污染物的污染时,在外加电压作用下其表面的泄漏电流比干净的表面要大得多。该泄漏电流产生的热量蒸发潮湿污染物,使绝缘基材的表面处于不均匀的干燥状态,导致基材表面形成局部干燥点或干燥带。干区使表面电阻增大,这样电场就变得不均匀,进而产生闪络放电。在电场和热的共同作用下,绝缘材料表面碳化,碳化物电阻小,促使施加电压的电极尖端形成的电场强度增大,因而更容易发生闪络放电。线路间反复发生闪络放电产生电火花,进而形成炭化导电电路的痕迹,破坏基材表面绝缘性能,形成导电通道,产生漏电起痕。CTI即是反应绝缘材料表面在有电位差存在下形成碳化导电通路,使之失去绝缘性能的指标。CTI值越大其耐漏电起痕指数越高,绝缘性越好。
普通的FR-4板材其CTI值一般在200V左右,而高CTI板材一般要求CTI≥600V,也有要求CTI≥400V。对于CEM-3和CEM-1板材也有高CTI的要求。
高CTI板材可通过选用特种环氧树脂、高耐漏电起痕性材料和玻纤品种,改进产品结构和工艺,如降低环氧树脂的Br含量,采用氢氧化铝作为辅助阻燃剂等。高CTI的FR-4覆铜板和高CTI的CEM-3覆铜板,适合制作高压、高温、潮湿、污秽等恶劣环境下使用的电子电气设备用印制电路板,能显著提高电子电气设备的使用安全可靠性。 6.不流动粘结片
近年来挠性覆铜板(FCCL)迅速发展,推动电子产品向“轻、薄、短、小”方向发展,与此同时刚挠结合印制板发展越来越快,性能要求也越来越高,以前刚挠结合板多采用的纯胶片(bonding sheet)由于材料本身的尺寸稳定性差,以及耐热性也越来越难于满足刚挠结合板的高耐热等性能要求。因此,很多PCB厂家寻求用于刚性板与挠性板之间联结用的其它替代材料,目前表现较好的替代材料为不流动半固化片(No-Flow Prepreg)。
不流动粘结片浸渍、干燥生产工艺可与常规FR-4半固化片的生产工艺参数实现兼容,主要区别在于两者配方树脂体系不同而控制指标有根本差别,尤其是流动度指标,不流动粘结片可以在0.1-0.5mm之间精确控制,而且不会影响优良粘合性、耐热性等综合性能。
刚挠结合印制板加工工艺:
(1)不流动粘结片韧性极好,剪切等各种操作过程几乎不掉树脂粉,适用于在压板前对不流动粘结片材料进行开窗操作;可采用锣机进行开窗,为防止刚挠印制板层压时开窗口处的流胶,刚性半固化片的窗口应比刚性外层的窗口稍大(一般比刚性外层的窗口大0.2-0.4mm为宜),且刚性半固化片越厚,刚性半固化片的窗口比刚性外层的窗口也应越大。在开窗口时注意将刚性外层或刚性半固化片钉紧,并用皱纹胶固定以免所开窗口边缘不整齐或尺寸与设计不符。
(2)由于不流动粘结片流动度很低,而且凝胶化时间(Gel time)非常短,通常压板过程中要求升温速率比较快,一般控制在2.5-3.5℃/Min为宜,同时采用一步加压,材料压力一般在300-400PSI即可。 7.高尺寸稳定性覆铜板
多层印制板制程有一种作法是内外层均先做好,然后用半固化片铺于多层之间,于热压机上热压将各层粘结成一块板。再经钻孔、孔金属化等到工艺流程,就制成多层印制板。也有先作内层,用半固化片将各内层连结,在最外层的半固化片上覆上铜箔,于热压机上热压将各层粘结成一块板后,再经钻孔、孔金属化、制外层图形等工艺流程,就得到多层印制板。不管采用何种制法,都是将各内层板粘结起来后再通孔连接。这就要求层压后各层板孔位必须对得很准。当前PCB制作技术已很先进,从工艺上保证压合过程中多层孔位对准已没有任何问题。但实际生产中,常出现内层制作完了以后,多内层孔位已对不准。这一现象,对于大焊盘、粗线条PCB板,只要孔位偏移仍在焊盘内,则尚可以将PCB制作继续作下下去。但对线条、导线宽度、间距趋于0.1mm,孔径向0.1~0.3mm,孔环宽度0.2mm或更小时,孔位稍微偏移就会造成孔金属化不能将各多层连接起来,造成废品情况出现。而这时,印制板制程已作了一大半,它不仅造成直接废品,增加成本,而且会影响成品率,影响交货期。因而,各PCB厂对覆铜板及半固化片尺寸稳定性极为关注。
除了多层印制板要求覆铜板有较高尺寸稳定性外,随着新型安装技术,如BGA、CSP、倒芯片安装等技术的发展,元器件的引脚数目更多,安装密度加大,如果覆铜板尺寸稳定性不好,就会影响电子元器件接插不到位,或因安装变形而影响整机效果。
以往,PCB制作前,是提前弄清楚该批覆铜板尺寸变化率,在图形制作时依据这个变化率加上修正量,以使制出PCB多层板不会产生对位时错位问题。也保证作出电路图形与原图是一致的。但有时,经过修正了的图形制作多层板仍有对位错位问题,这说明每批覆铜板尺寸变化率有差异,即质量一致性不好。因此,提高覆铜板及半固化片尺寸稳定性应该与尺寸变化率一致性是同一概念。因为绝对没有尺寸变化的覆铜板是没有的。覆铜板技术工作者的工作目标是减少覆铜板尺寸变化率及保持每批产品尺寸变化率一致性。
覆铜板尺寸稳定性虽然与生产工艺有关,但主要还是取决于构成覆铜板的三种原材料——环氧树脂、玻纤布和铜箔。当前FR-4型覆铜板所用的这三种原材料热膨胀系数(CTE)相差较大,因而制出产品尺寸稳定性不能适应精细线路及高多层印制板制作要求。在这三种材料中,以环氧树脂的CTE为最大,所以在研制高尺寸稳定性覆铜板时,往往先从环氧树脂入手。
(1)通常FR-4型覆铜板是用双官能环氧树脂,它的CTE比较大,产品Tg在130℃附近。而PCB加工制程许多操作温度均超过130℃,因此会出现较大尺寸变化。采用多官能环氧树脂与双官能环氧树脂併用或完全替用是提高产品Tg常用的一种作法。采用多官能环氧树脂以后,由于固化体系交联密度提高,Tg会提高,产品尺寸变化相应就会减少。当产品Tg值高于180℃时,已高于PCB制程中大部分工序操作温度,包括多层板热压成型温度。因而其尺寸变化就不会影响到精密图形及高多层印制板制作要求。
当前,科学工作者已发现了不少固化过程体积收缩变化非常小的新材料。新材料的出现与如何把它用到覆铜板生产中来,是并用还是单独用,并使其具有工业化生产价值,是覆铜板科技工作者需要继续探索的工作。
加入填料以提高制品尺寸稳定性,是塑料行业及其它行业常用的一种方法,它对覆铜板行业也是合适的。只是选用添料种类及使用方法有所不同而已。填料可以采用无机填料,为了增强其与环氧树脂结合力,应当选用合适偶联剂或更新的树脂,无机填料间的界面处理技术,对无机填料表面进行处理,使无机填料更好地分散在树脂中,达到高分散、高粘接作用。经过合理的表面处理以后,虽然适当增加填料比例,也不会因填料加入而造成胶液粘度增大,覆铜板工艺性下降,也不会由于填料加入而降低粘结片树脂流动度,成型时板内空隙率增大等情况。产品的尺寸稳定性,Tg值得到提高,吸水率明显下降。基板表面由于有填料充填于玻纤布表面,及玻纤布网格间,减少通常FR-4型覆铜板因树脂固化收缩时而形成玻纤布网格内略低陷,结点略高,基板表面粗糙度较高的问题。基板面平滑度提高有利于PCB精细线路制作与适应电子产品新安装技术需要。
(2)在基板中,玻纤布的含量超过50%。因此,基板尺寸稳定性提高,除了对CTE变化最大的环氧树脂进行改性之外,玻纤布的影响也不能忽略。当前FR-4型覆铜板所用E-玻纤的CTE为5.04ppm/℃,而S-玻纤的CTE为2.34 ppm/℃。因而采用S-玻纤布代替E-玻纤布,可以制得高尺寸稳定性覆铜板。但由于S玻璃的SiO2和Al2O3的含量高于E-玻纤,使基板的机械强度更高,机械加工难度加大,钻头磨耗率加大。因而,S-玻纤布在当前未有大量推广。但有厂商仍在继续开发保留S-玻纤CTE低特性,提高其PCB机械加工性能玻纤布新品种。对于玻纤布与覆铜板产品尺寸稳定性方面工作在E-玻纤布的结构改造方面作得较多。如针对玻纤布在上胶机上胶过程中经向受张力大于纬向,造成覆铜板尺寸变化经向大于纬向。因而,不少玻纤布生产厂与覆铜板厂密切配合,对玻纤布经纬密、纱线结构等进行调整,改进。以减少覆铜板经纬方向尺寸变化差异。也有的厂家采用双股经纱,双股纬纱交织,仍为平纹结构,布面经开纤处理。这种布特点是减少了玻纤布面孔隙率,提高了玻纤布玻纤体积充填率。因而有利于基板尺寸稳定性提高。
使用开纤布,在一定程度上能提高基板尺寸稳定性。因为玻纤布表面经开纤处理以后,空隙率减少,玻纤分布均匀性提高,树脂浸透性提高。因而有利于提高基板尺寸稳定性,也提高了基板表面平整性及微通孔质量可靠性。
由于构成覆铜板的三种材料中,以玻纤布的CTE为最小。因此,提高玻纤布所占比例(也即降低树脂含量),有利于提高基板尺寸稳定性。但树脂含量降低,会影响基板电绝缘性能,耐化学药品性能等。
因而在改进基板性能时,不能顾此失彼,一定要考虑产品综合性能。当前,已有更多不同规格型号、不同特性用途的玻纤布供用户选用,以适应各种不同特性要求PCB制作。如过烧布可减少钻头磨损率,提高孔壁光洁度。石英玻纤(Q玻纤)介质损耗更小。混织布(E-玻纤与有机纤维混织)由于某些芳酰胺型具有较低CTE及较低ε,所以将其纤维与E-玻纤混织,可以起到降低产品介电常数,又起到提高尺寸稳定性作用等等。但有的布可能是专一用途,专一目的。有的布则可能有多种用途,在新产品试制中应充分予以利用。
(3)铜箔对覆铜板尺寸稳定性影响相对较小。因为在PCB制程中,大部分铜箔被蚀去,因而铜箔对基板尺寸稳定性影响比其它两种材料要小得多。但在实际生产中,其影响仍是不可忽略的。特别是在多层板生产,铜箔的比例相应就高了不少。当前,覆铜板行业中较常用的电解铜箔的三个型号及特性见表7-8-3。
表7-8-3
型 号 |
国际上代号 |
延伸率%(最小值) |
1/2 OZ |
1 OZ |
2 OZ |
23℃ |
180℃ |
23℃ |
180℃ |
23℃ |
180℃ |
标准电解箔 |
STD |
2 |
|
3 |
|
3 |
|
高延展性电解箔 |
HD |
5 |
|
10 |
|
15 |
|
高温延伸性电解箔 |
HTE |
2 |
2 |
3 |
2 |
3 |
3 |
当采用高温延伸性电解铜箔时,产品在热压成型时铜箔能较好地配合树脂流动,因而在一定程度上有利于提高产品的尺寸稳定性。同时制品如凹坑之类外观缺陷也有相应减少。对于多层PCB用的芯板,应尽量使用THE铜箔。
(4)生产工艺:对基板尺寸稳定性影响虽不是关键因素,但仍是有一定影响。包括上胶时张力问题;层压时升降温速率问题;每叠合中产品数量,每块产品温差问题;垫板材料与不锈钢板导热系数及厚度搭配问题;不锈钢板热膨胀系数与产品热膨胀系数差异问题等。如果搭配得好,处理得好,对提高基板尺寸稳定性有一定作用。
总之,提高基板尺寸稳定性可以选用的路线很多,实际应用时,可以只选用其中一种。如果采用多官能环氧树脂,同时添加适量填料,必要时选用某些有助于提高基板尺寸稳定性玻纤布与之相配合等。
8.高多层、精密印制电路用超薄型覆铜板
电子产品的轻、薄、短、小、高密度组装,促使印制电路板向多层、高多层方向发展。根据高多层PCB生产需求,用于高多层印制板基板厚度范围为0.02~0.127mm,这就是通常所说的超薄型覆铜板。它对应于当前最薄型玻纤布101型(单位面积质量16.3g/m2,标称厚度0.024mm)、104型(单位面积质量18.6g/m2,标称厚度0.028mm)、106型(单位面积质量24.4 g/m2,标称厚度0.033mm)及1080型(单位面积46.8 g/m2,标称厚度0.053mm)。超薄型覆铜板是一类很有发展前景覆铜板品种。超薄型覆铜板应和超薄型半固化片配套供应,以防止不同厂商材料CTE不同而影响多层板层间对位精度。高多层印制板,高密度组装技术,必定要求细线条、小孔径、小焊盘的精密印制电路板用途。因此,超薄型覆铜板不能以普通FR-4的条件生产。用普通FR-4的条件生产出来的超薄型覆铜板,从耐热性、尺寸稳定性、精密电路加工性都满足不了要求。
高多层、精密印制板电路用途超薄型覆铜板生产,对粘合剂、基材、铜箔、生产设备有较高要求。
为了保证多层板各层间图形不变形,不错位,需要基板有较小的CTE或较高的尺寸稳定性。即在一定CTE条件下,批与批间产品尺寸变化应尽量一致。基板所用的粘合剂应有较小的CTE。最常见做法是采用高Tg材料或耐热性较好的材料。由于高密度组装,将产生较大热量,因此,基板应有较高耐热性,才能保证基板热态下性能X、Y及Z轴有较小膨胀系数,以保证金属化孔的可靠性。
超薄型覆铜板用基材很薄,特别是106及104型玻纤布非常薄,极容易变形。因此立式上胶机烘箱不能太高,多数采用5m高的烘箱。对于7.5m高的烘箱,要用于104型玻纤布上胶,有一定难度。除了立式上胶机烘箱不能太高之外,上胶机采用低张力装置,开卷必须采用变频电机主动开卷,才能保证薄玻纤布不会产生变形。对于层压设备,也必须采用高精度层压机,层压机热压板平行度、平坦度偏差应比普通压机更小,才能保证压制产品具有较高厚度精度。不锈钢板及托板材质、厚度、厚度偏差、不锈钢板CTE等都必须密切配合,才能使超薄覆铜板生产质量得到保证。
超薄覆铜板由于很薄,所以在分板、裁切、测厚、外观检验、包装等操作都与通常覆铜板有所区别。如分板时不宜用手工操作,以免板材变形。而在用移板机分板时,吸盘的吸力也不能太大。通常吸盘吸移超薄覆铜板时,会将板吸变形或留下吸盘印。这都是不允许的。通常可采用小吸盘或吸与夹并用方法。裁切时,压紧装置压力要调得较小,以免留下压痕。对于超薄板,用辊切更适合些。超薄覆铜板包装时,在板两边宜用刚性合板垫在产品两边,以防运输中产品变形或受到挤压等。
由于超薄覆铜板很薄,热压时传热较快,成型时间可以较短。因而,对于超薄覆铜板生产,一些覆铜板厂采用连续层压生产工艺。将成卷粘结片与成卷铜箔在连续生产压机上热压复合而成。它较一张张地叠合,层压生产工艺,明显提高了生产效率。由于薄板相当容易变形,连续层压可以减少多道工序造成的废、次品,有利于降低产品成本。连续层压制程主要缺陷是制品在层压机中停留时间比较短,会造成产品固化不十分充分情形。对于要求比较高的场合,连续层压产品应进行后固化处理,以使树脂充分交联固化,使产品性能得到保证。
超薄覆铜板由于容易变形,包装及运输时应予以充分注意。通常,可以采用于每小包产品上下加刚性板方法,并予以密封、防潮包装。这样的包装也适宜于长途运输。
超薄覆铜板及半固化片大多采用104、106及1080玻纤布。这些玻纤布很薄,生产中很容易变形。生产中如何防止玻纤布变形及保证其树脂含量均匀性、固化度一致性是上胶时要很好解决的问题。为了提高基板面平滑性,以适于精密、细线条印制电路板制作,必要时基板制作可采用开纤布,它使玻纤布表面经纬纱扁平化,提高树脂浸透性和基板面平滑性。同时也掩盖了平纹玻纤布结点和孔隙,避免了PCB钻孔时,钻在玻纤布交叉结点上与钻在玻纤布空隙上孔壁光洁度不同及导通质量情况不同等缺陷。
但由于环氧玻纤布覆铜板难以实现激光蚀孔。因而,对于细孔微孔径高精度PCB板,可考虑采用有机纤维(如芳酰胺类等)制作的覆铜板。
超薄覆铜板多数用到薄型,低轮廓或甚低轮廓电解铜箔。当前,用于覆铜板生产用铜箔的厚度有5μm、9μm、12μm、18μm、35μm、70μm、105μm等。超薄型覆铜板多数用18μm以下厚度铜箔。但由于5μm、9μm铜箔太薄,操作上难度较大,因而须有载体。如以铝箔为载体,在PCB制作前,再将载体撕去或蚀去。但当前5μm、9μm超薄铜箔用量仍较少,而低轮廓及甚低轮廓铜箔应用发展则相对较快。由于此种铜箔晶体结构与普通铜箔有差别,它对外力承受力较好,而且有较高热稳定性,不会由于高多层板制程中多次层压而产生铜的结晶。蚀刻时间比普通铜箔短,而且不会有侧蚀及铜粉残留等现象发生。因而适于高精细线路,高多层印制电路板应用。
在精密印制电路制作时,也用到“双表面处理”铜箔。此种铜箔是将铜箔光面进行粗化处理,而使铜箔有两个处理面。在压制覆铜板时,将由光面制作的粗化面朝向基板而由电解铜箔毛面形成处理面则朝外,用于印制电路图形。这种铜箔突出特点是可减少侧蚀,及做内层板用途时,由于其已具有经过处理的毛面,所以可以不必经棕化、黑化处理,或可提高棕化、黑化处理效果,提高内层板层间结合力。
9.低介电常数覆铜板
随着电子技术迅速发展,信息处理和信息传播速度提高,为了扩大通讯通道,使用频率向高频领域转移,它需要基板材料应具有低介电常数(ε)与低介电损耗角正切(tgδ)。只有降低ε值,才能获得高的信号传播速度,及只有降低tgδ,才能减少信号传播损失。
覆铜板的介电常数和介电损耗角正切取决于基材和粘合剂。普通FR-4型覆铜板用E-玻纤布ε较高,在1MHZ下,达到7.23,而环氧树脂的ε值为3.9。因而降低基材ε是降低基板ε的最有效方法之一。玻纤布的介电常数与玻璃组分相关。如以纯SiO2制成的玻纤布(俗称石英玻纤),其介电常数仅为3.89,而D玻纤为4.74,S玻纤为6.25。在玻璃组分中,SiO2的含量越高,则ε值越低,但玻纤布的硬度也随SiO2含量升高而增大。在PCB制程中机械加工难度加大,成本也高了许多。因此,在实际生产中,很少用石英玻纤布来制造低介电常数覆铜板。用其它类型,介电常数较低玻纤布来制造低介电常数覆铜板,则需对玻璃组分进行调整,以使玻纤布织造性及其在PCB制程中可加工性有较大提高。为了提高SiO2含量较高玻纤布织造性及其在PCB制程中可加工性,有些玻纤布厂开发了玻璃纤维和低介电常数的有机纤维(如芳酰胺纤维、聚醚醚酮纤维、聚醚酰亚胺纤维、聚砜纤维等)混纺布或混织布或纯有机纤维布。虽然,这些新型基材仍未得到广泛应用,但由于降低基材介电常数是降低制品ε最有效方法,因而,会成为研制的重点。
当前,在低ε值覆铜板研制中,低ε树脂的研制进行得比较活跃。比较经典的低ε覆铜板是采用聚四氟乙烯树脂作为粘合剂,由于聚四氟乙烯具有甚低介电常数(ε=2.1)及优良介电性能,耐高温性能,所以最早被用作高频用途覆铜板。但由于聚四氟乙烯是一种非极性热塑性材料,出其本身价格比较昂贵外,覆铜板制造工艺难度很大,难以按传统覆铜板生产工艺进行生产,层压温度要求也很高,而且板材空间粘合性很差。这些都限制了聚四氟乙烯覆铜板的发展。
以聚丁二烯这一类树脂来制造高频用途覆铜板,这一工作一直未停止过。由于聚丁二烯也具有较低介电常数(ε=3.0),这一类材料价格比较便宜,容易取得。在覆铜板制程工艺性比聚四氟乙烯树脂好,热压成型温度比较低。所以具有开发价值。但聚丁二烯也是非极性等缺陷。因而未能广泛应用。
以聚苯醚树脂制造高频用途覆铜板近年来取得较大进展。聚苯醚树脂(简称PPO或PPE)的介电性能(ε=2.5)仅次于聚四氟乙烯树脂,而且耐热性很好。因此,用聚苯醚树脂开发低介电常数及耐高温覆铜板工作受到很多覆铜板厂重视。聚苯醚树脂也是一种热塑性材料,在聚苯醚树脂应用上,多数采用对其进行改性,使之成为热固性。也有采用与其它覆铜板工艺性能好的树脂(如环氧树脂、BT树脂等)共混的办法,使体系形成“互贯穿网络固化体系”。由于以聚苯醚树脂制造的覆铜板原材料价格不是很高,覆铜板工艺性能与传统方法相接近,而且产品的介电常数较低,耐热性,尺寸稳定性也相当优良,因而被众多覆铜板厂所重视。
聚酰亚胺树脂,BT树脂也具有较低介电常数,可作为高频覆铜板用途。但由于其耐热性更加突出,所以常常用于耐高热覆铜板用途。
尽管可以作高频用途覆铜板的低介电常数材料很多,但不管从材料成本、传统覆铜板工艺性,PCB制程工艺性都仍不及环氧树脂。因此,在当前高频用途覆铜板研制上,有不少覆铜板厂仍着力于环氧树脂的改性研究。环氧树脂的介电常数为3.9。高分子材料介电常数与分子极性相关,极性小的材料其介电常数相应也较小。如果在环氧体系中,引入用某些极性低,大取代基的树脂或固化剂,使聚合反应时,能消耗掉环氧树脂上强极性基团,以降低固化物极性基团含量,就可达到降低环氧树脂体系介电常数的目的。如在环氧树脂结构中引入烷基结构或用脂环族改性酚醛树脂,氰酸酯树脂(ε=2.9)与环氧树脂反应,或对环氧树脂上羟基进行醚化等,都可制得具有较低介电常数,且综合性能优良的覆铜板。
二、无溴阻燃型玻璃布基覆铜板
(一)、概述
阻燃性是FR-4类覆铜板的关键性技术指标,本章第二节已介绍,其阻燃性是通过在树脂溶液中的溴化环氧树脂(溴含量19~12%)及含阻燃元素固化剂实现的
如本书第六章第六节指出,由于欧盟的RoHS指令禁止在电子产品中使用多溴联苯和多溴联苯醚,以及国际上有些研究机构研究发现,溴类阻燃剂在燃烧过程中,会释放出一些对人体健康和环境有害的物质(如二噁英等)。因此,近年来电子整机便要求使用无溴印制电路板和无溴覆铜板。这种呼声,在欧洲尤其强烈。
又由于溴元素是处在元素周期表中第Ⅶ族(F、Cl、Br、I)的卤族元素,所以业界一般也把无溴覆铜板称为无卤覆铜板。
在无溴阻燃型覆铜板开发时,应考虑以下四方面的基本要求:
1、产品不含有卤素或被认为有害的物质。
2、对产品原有性能无产生消极影响。
3、产品成本,不应过大增加。
4、工艺可行,可量产化。
从化学角度考虑,在元素周期表中,具有阻燃功能的元素,除卤族元素外,还有Ⅴ族的N、P、As、Sb、Bi及Ⅲ族的B、Al等元素。
若在树脂体系中,引入N、P等元素,使其按一定比例配合,利用其相互之间的协同效应,达到阻燃效果。实践证明,通过这种工艺路线,可以获得较理想的阻燃效果。
(二)、无卤化FR- 4型CCL主流树脂组成配方及其技术的推进
1、无卤化FR- 4型CCL主流树脂组成配方的特点
当前,世界无卤化FR-4的主流树脂组成配方,是以含磷环氧树脂做本体树脂,酚醛树脂做固化剂,加上一定量的无机填料,三者所构成它的主成分 。 其中无机填料加入的比例量,要比一般无铅兼容性FR-4多;为协助本体树脂的阻燃,无机填料的种类多选择氢氧化铝。这一树脂组成配方特点,也决定了所制成的无卤化FR-4“脆性大”问题成为需要克服、解决的普遍技术课题。
2、技术推进的三个阶段
无卤化FR- 4技术发展的第一阶段,是采用DOPO等有机磷化合物合成含磷环氧树脂(作为本体树脂)、酚醛树脂(作为固化剂)的树脂组成配方的确立。在它的树脂组成配方组成上运用无机填料技术走向成熟,可认为是它的技术发展的第二阶段。自21世纪初起,世界无卤化FR- 4型CCL的厂家,在主流树脂组成配方中,大多数采用了(有的是新增)无机填料(主要以氢氧化铝为主)作为填充。它一方面起到协助含磷环氧树脂阻燃的作用,另外还起到降低板的Z方向热膨胀系数、提高弹性模量、板的表面平滑度的功效。
近年来,在对无卤化FR- 4技术又有了新的认识提高:一方面,发现它典型的树脂配方还可以带来更多性能提高的贡献,例如,它对板的耐热性提高;对介质损失角正切的降低等都是原传统FR-4型CCL所未能达到的。另一方面,与无铅兼容性FR-4相似的暴露出它的性能弱点(微孔加工性、吸湿后耐热性等),是需要在此方面性能的改进 。为此,无卤化FR- 4技术又推进到第三阶段。这阶段的技术水平其特点是,它的性能均衡性获得明显的提高。无卤化FR- 4型CCL树脂各组成成分的增多(与一般FR-4相比),加大了它的开发与工艺控制的难度,如何发挥各个组成成份在性能上的相互补充、配合,成为此阶段开发这类CCL技术上的新课题。
有的专家预测 ,未来实现树脂组成的无卤、无磷化,将推动无卤化FR- 4技术进步到第四发展阶段。尽管目前已有实验室规模的此方面研究成果发表,但真正实现大生产,并达到低成本、性能的均衡性,还要在若干年以后。
(三)新型原材料的采用及其对无卤化CCL性能提高的贡献
1、总述
在无卤化FR- 4结构组成上采用了许多新型原材料。这主要包括:含磷环氧树脂、其它高分子树脂;无机填充料;酚醛树脂等固化剂;开纤玻纤布;专用电解铜箔等。它们代表着CCL用原材料在近年技术进步的新成果。它们在确保、提高无卤化FR-4性能方面作出了重要的贡献(见表7-8-4),是无卤化FR- 4技术的重要组成。表7-8-4 围绕着无卤化FR- 4型CCL性能提高各种原材料所赋予的贡献
表7-8-4 各种原材料对通过无卤化FR-4性能的贡献
原材料种类 |
对无卤化 FR-4 型CCL性能提高的贡献方面 |
含磷环氧树脂 |
确保及提高耐热性、阻燃性、介电性能、粘接性等 |
其他特种高分子树脂 |
少量加入,以提高板的柔韧性,提高树脂与纤维增强材料界间的粘接性等 |
无机填料 |
协助阻燃,降低板 Z 方向膨胀系数、提高耐热性 |
酚醛树脂等新型固化剂 |
提高耐热性、阻燃性、粘接性; |
高开纤玻纤布 |
提高树脂的浸透性、均匀性,以弥补钻孔加工孔壁不光滑等问题 |
无卤化 CCL 专用铜箔 |
解决无卤化 CCL 由于半固化片中树脂含量低而造成的铜箔剥离强度偏低的问题。 |
2、含磷环氧树脂及其它高分子树脂
20世纪90年代中后期, 日本CCL业通过几年的实验研究认识到, FR-4型CCL实现无卤的阻燃,最好途径是树脂组成成份中含有可参加反应的含磷树脂。日本一些CCL厂家在探索含磷树脂合成工艺的过程中,曾用环氧树脂与磷化合物、苯基膦酸化合物等进行合成含磷阻燃树脂 ,但它们共同存在着成形物(制成的CCL)吸水率高、板的脆硬、吸湿后浸焊耐热性低等难以解决的问题。而DOPO、ODOPB等有机磷化合物合成含磷环氧树脂的工艺路线则脱颖而出,在多个合成反应型含磷环氧树脂方法中,成为较为成功的、较适应于无卤化CCL性能提高的合成路线。台湾成功大学工程研究所的王春山等 ,在世界上也率先开展了这条合成含磷环氧树脂的工艺路线研究。并把这项成果较早的应用到CCL树脂组成物中。这也为以后台湾的部分CCL厂家在无卤化CCL的研发、生产上能够较快的跟进日本的前进步伐,提供了有利条件。
近几年含磷环氧树脂及其主要原料(DOPO、ODOPB等)制造技术已走向成熟 。我国一些大学及研究院所近年也在这方面研究中涌现出不少的成果,国内无锡阿科力化工有限公司等在含磷环氧树脂生产与应用方面都获得较大的成果。
无卤化FR-4技术发展到第三阶段,要求含磷环氧树脂能够在与其它树脂成分很好配合,特别寄于它对降低CCL吸湿性、提高树脂体系固化物的柔韧性、降低CCL材料成本等贡献方面,今后会有更好表现。
整个无卤化FR- 4型CCL树脂体系中,还需要含磷环氧树脂以外的高分子树脂的配合。它们主要担负着通过进一步提高树脂耐热性,
降低A阶段树脂体系的粘度(热态熔融粘度较高的含磷环氧树脂在整个树脂组成物中的比例较大时,加之大量的无机填料的加入到树脂体系中,都会造成整个树脂体系的粘度很高。而树脂体系粘度增大,会造成半固化片加工上的困难及板品质的下降) [25] ,提高树脂体系的柔韧性等功效。
3、无机填料
近年来,在实现PCB基板材料的无铅化、无卤化的进程中,无机填料(Filler s)在CCL中的应用技术得到了飞跃性的进步。适应CCL性能要求的无机填料品种在纷纷涌现、无机填料的性能在不断提高、新型无机填料表面处理技术的层次在不断提升,配合它在CCL使用的混胶、浸胶设备在不断的改进。
在当前PCB市场更加注重高“性价比”的背景下,无机填料在降低板的厚度方向膨胀系数方面,贡献突出,不易用其它技术手段所替代。从提高CCL无卤阻燃性的角度考虑,选择无机填料品种的首先看重的,是需要它发挥其协助阻燃的功效。因此,无卤化CCL中所用无机填料,更青睐于选择氢氧化铝品种。这是由于它在燃烧中起到吸热的作用,以及热分解时分离出水而起到降温的作用,所以它的阻燃协效性相对其它无机填料更好些。
对于氢氧化铝填料应用于无卤化CCL中的研究开展,表现在多个方面。从近年来日本CCL厂家研究此方面的专利内容中可看出:①从品种的研究课题来讲,有对高纯氢氧化铝、高耐热氢氧化铝、柱状氢氧化铝等的专题研究。②从氢氧化铝的性能指标对CCL性能影响方面的研究来讲,可归纳有:对氢氧化铝的最小粒径含量、平均粒径、粒径分布、开始脱水温度、比表面积、NaO含有率、硬度等各个性能项目对CCL性能影响的研究。③从对无机填料的表面处理的研究课题来讲,有选择处理剂品种、对各种硅烷偶联剂结构上的改善、偶联剂加入方式、偶联剂添加量、偶联剂处理液pH值的控制等的研究。④从实际应用工艺手段来讲,还包括:氢氧化铝加入树脂体系的方法、配比量、与其它无机填料(如硅微粉等)配合的工艺技术、相关检测技术及评价方法等的研究等 。
在CCL结构组成中引入一种新材料的研究,总是围绕着两个侧面展开:一个侧面,是将它在CCL所担当某一项性能提高的“重任”,如何更好的实现;另一个侧面,由于该材料的导入,会对CCL其它一些性能产生负面影响,如何设法将其限制到最小的程度。达到这两个侧面的比较完美整合,可算在技术上提升到了一个新层次。
对新材料应用研究的深入,是要达到这一材料能发挥它对CCL的其它性能提高的功效(即可称为“第二功效”、“第三功效”┈┈)。随着这项应用技术研究的不断推进,此课题的研究重点也有所转变,研究层次也在提高。例如20世纪90年代,日立化成研究的无机填料,主要重点解决是辅助阻燃性的提高、降低线膨胀率问题。21世纪初(约在2000年—2003年),主要研究的重点目标,是提高钻孔加工性、提高绝缘可靠性方面。近年来,研究重点目标是提高CCL的耐热性(由无机填料的高填充料所引起的等)、薄形化CCL的提高刚性(提高弯曲模量)问题等。
4、玻纤布
无卤化FR- 4要比一般FR-4在钻孔加工中易出现孔内壁裂纹和树脂脱落的问题。如果在孔内壁产生裂纹,就易产生电镀液对孔内壁的浸蚀、污染,从而诱发了绝缘可靠性的下降(见图7-8-3)。另一方面,基板材料树脂的脱落,孔内壁粗糙度的增大,导致孔内壁电镀铜层的不均匀,在冷热循环环境条件时,产生应力集中,导致易造成导线断线的现象发生。一些研究成果表明,造成上述的原因主要来自两方面:其一,由于有无机填料加入到树脂体系中,使得本体树脂比例量的相应减少,引起玻纤布与树脂界面粘接性下降。其二,由于一般无卤化CCL用树脂刚性结构过多 , 在它的机械钻孔加工中,造成了CCL的玻纤布与树脂界面的剥离,以及由此产生的裂纹和树脂脱落。 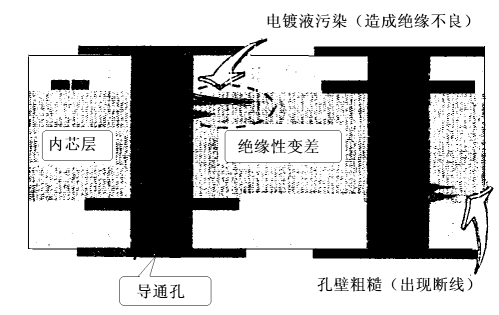
图7-8-3 对孔加工性品质的影响
PCB的钻孔加工,实际上是给了基板一个切削冲击力。CCL的玻纤布与树脂界面的粘接性差异,造成钻孔加工中高速运转的钻头所产生的切削力在基板内传递方式上的不同。界面粘接性高的覆铜板是通过玻纤布按照钻头深入的方向来传递切削力的,这种切削力的传递方式,有利于钻孔加工后形成孔内的光滑壁面。而界面粘接性低的覆铜板,基板层间已产生的裂纹,切削力的传递途径是沿着层间的裂纹进行,并起到扩大裂纹,加深界面的剥离的效果(见图7-8-4)。 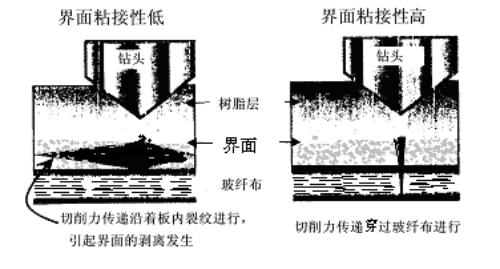
图7-8-4 钻孔加工性发生质量问题的解析
改进玻纤布偶联剂处理性能及采用高开纤玻纤布,都是提高无卤化FR-4的玻纤布与树脂界面粘接性的重要手段。
在此方面,日立化成工业株式会社近期发表的有关研究专利提出:采用高开纤处理玻纤布,以解决激光或机械钻孔加工质量(微孔的内壁表现粗糙等)提高的问题。他们采用的60μm厚(IPC-4412标准中的1080、1078规格),其通气度为20-60cm3/cm2/s。这种高开纤玻纤布不仅要达到高通气度,而且需要达到断裂强度、布厚度的高均匀一致性。
5、酚醛树脂固化剂
自无铅兼容性FR-4及无卤化FR-4开发、应用以来,世界CCL业(特别是日本、台湾等CCL业)十分青睐于将酚醛树脂充当这类CCL树脂体系中的固化剂成分,以代替传统使用的双氰胺(Dicy)固化剂的工艺路线 [30] 。酚醛树脂固化剂在提高无卤化FR-4的耐热性、阻燃性、粘接性上发挥了重要的作用。同时,许多研究证明,酚醛树脂固化剂与由DOPO、ODOPB为原料合成出的含磷环氧树脂的“搭配”,会产生比双氰胺有更好的固化反应的效果。在大日本油墨化学工业公司中从事多年酚醛树脂固化剂研发的一位专家曾提出 : “ 覆铜板树脂用酚醛树脂固化剂,要完成赋予酚醛树脂具有提高板的耐热性、粘接性及非卤化的阻燃性;同时,它还要达到降低吸湿率;改进介电特性(低介电常数化);达到低应力、低膨胀(低收缩)等性能的要求。”此话较准确的指出了作为酚醛树脂在“扮演”无卤化FR-4树脂体系的固化剂的“角色”中,对它的“扬长”和“避短”的两方面要求。
酚醛树脂固化剂现已成为提高无卤化FR-4性能的研究重点方面。为此,它的制造技术也在近年得到很大的进步。如出现了含氮酚醛树脂、低吸湿性酚醛树脂、柔韧性得到改善的酚醛树脂、高纯酚醛树脂等。世界有的CCL厂家在无卤化FR-4树脂组成体系中开始尝试酚醛树脂与双氰胺并用的固化剂技术途径,得到业界的关注 。
(四)、对两例无卤化FR- 4开发成果的技术浅析
近年来,国内外在无卤化FR-4方面的论述很多。据统计,日本松下电工和日立化成的无卤化FR-4在2007年世界同类CCL市场的占有率分别是28.3%和17.5%, 是世界第一大和第三大的无卤化FR-4供应厂商 。他们开发的无卤化FR-4产品,在技术上的创新很有特色。
1、松下电工的开发实例
在日本,松下电工是较早投入含磷环氧树脂的合成及应用这项技术研究工作的CCL厂家之一。其研究目标开始就很明确:将它作为主阻燃树脂用于无卤化FR-4覆铜板中。
90年代末,除松下电工之外,日本还有不少的环氧树脂厂家(如东都化成、大日本油墨、日本化药等)也作了这种环氧树脂的研发工作,其它日本CCL生产厂家(如住友电木、东芝化学等)几乎也在同一时期也作了大量的此树脂在CCL上的应用研究工作。可是松下电工与日本其他环氧树脂生产厂、覆铜板生产厂在开发思路上有所明显不同是:他们不仅注重DOPO、ODOPB类的含磷环氧树脂的应用,而且还开展独自开展这类含磷环氧树脂合成方面的研发工作。这使得到松下电工在DOPO、ODOPB类有机磷化合物合成含磷环氧树脂方面、掌握了关键技术,积累了更多经验。它的合成工艺、品质控制、性能调整、在制作无卤化FR-4型覆铜板中对树脂组成体系性能的影响等,松下电工都能够有更加深刻认识、更加自如的运用。现今,他们将这种“将含磷环氧树脂性能熔入到整个树脂组成体系中进行设计、控制”(松下电工研发人员语)的思路、作法,在无卤化CCL开发上已结硕果。
松下电工曾在近十年来发表了多篇应用含磷环氧树脂的无卤化CCL为主要研发内容的专利,将它较晚发表的(2007年发表)专利,与相隔五、六年较早发表的此方面的专利[38]相对照,不难发现:松下电工在多年开发和改进无卤化CCL中,贯穿着“在继承原有成果中,不断求创新和发展”的研发思想。“继承”——是在几年前的含磷环氧树脂合成技术的基础上,对本体树脂及其其它组份的性能上进行改进、提高。“发展”—— 具体主要表现在:在树脂组成物加入无机填料后,如何以确保它对抑制吸湿性、提高耐热性、确保阻燃性,降低 A阶段含磷环氧树脂的粘度(以达到增加无机填料添加量的目的)等方面,赋予含磷环氧树脂的新功能方面。例如,为达到上述对含磷环氧树脂性能提高的新需求,松下电工在对合成含磷环氧树脂中的醌化合物与磷化合物配合比上,不断获得研究新进展 。
这一实例,使我们得到这一个启发:将CCL本体树脂合成中的关键材料配合比与树脂分子结构、分子量大小、参加反应基多少、粘度大小等之间关系“研究透”,实际是掌握了对树脂作某些改性、某些性能提高的一种手段。
2、日立化成的开发实例
在日立化成工业公司的无卤化FR-4——MCL-E-679FG性能上,体现出它们在填料技术方面的创新 。
日立化成在开发无卤化FR-4过程中,开始同样遇到需要解决提高玻纤布、无机填料、树脂的界面的粘接性的难题。界面粘接性是直接影响着CCL的耐热性、加工性、绝缘可靠性等性能的重要因素。界面粘接性低下,在加热后产生裂纹会扩大、延伸,破坏界面(见图7-8-5)。
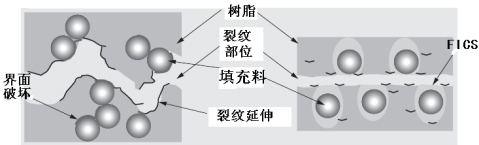
图7-8-5 对填充料FICS处理和未处理的两种CCL在加热后产生裂纹的延伸情况对比
日立化成采用界面控制技术(简称FICS技术,即利用偶联剂处理的技术)提高界面粘接性,去实现对玻纤布、无机填料、树脂的三者界面的有效控制,达到了三个方面性能的改善:即填充料在树脂中的分散性提高;高填充料加入量的情况下还能抑制树脂体系粘度的升高;对存在于树脂中的内应力起到缓冲的效果。
日立化成的FICS技术并非只是用偶联剂对无机填料做一般性的表面处理。实际上,这项技术主要包括着三方面的控制技术:即对处理剂向本体树脂的扩散及反应的控制;对形成界面层的各物理特性整合的均衡,进行的调整和控制,以及对树脂-处理剂的反应物分子骨架结构的控制(图7-8-5)。 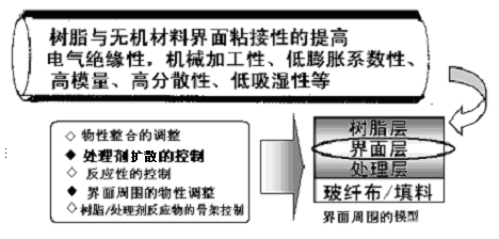
图7-8-6 覆铜板组成结构界面控制的概念
为了达到上述界面控制的更完美,他们还采用AE检测技术。固体物材料内部积储的能量,在它产生塑性变形或破坏时就会释放出来。一部分能量在释放行为发生时会出现弹性的波传播的现象,即表现为声发射现象。利用此原理建立了一种声发射检测技术(Acoustic Emission,简称AE)检测技术。声发射是一种物体破坏的前兆发出的超声波现象。AE法是通过测定超声波发射次数来考察其产生裂纹及其延伸的程度。AE检测技术是目前对复合材料的界面粘接性进行定量评价的方法之一。
对覆铜板结构组成界面的粘接性进行解析、评价。利用此检测分析方法,他们对界面粘接性与钻孔加工性之间关系、与绝缘可靠性(耐离子迁移性)之间关系,以及实现无机填料高填充量化的CCL品质等方面,做了大量的定量性解析研究 , 从而促进了无机填料在无卤化FR-4的应用技术提升到一个更高的层次。
图7-8-7反映了FICS处理与未处理的填料两种树脂结构的CCL经AE法测定到的产生裂纹及其延伸情况对比。 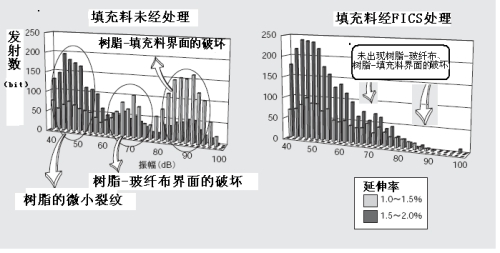
图7-8-7 填充料经FICS处理与未处理的产生裂纹及其延伸情况的对比
这一实例,使我们加深了这样两点认识:覆铜板关键技术的突破或一些重要性能的改善,往往依托于某些相关理论认识上的提高以及新的测试手段的运用。在当前覆铜板技术开发越来越追求低成本、高性能的背景下,“对CCL结构组成中的各个原材料有更高性能的集成,以及去挖潜各个原材料特性效率的课题研究更显得非常的重要(日立化成研发人员语)”。而在这项工作开展中, 像日立化成在无卤化FR-4中采用的界面控制的技术,会越来越发挥其重要的作用。
三、FR-5型覆铜板
通过提高基板Tg,以提高覆铜板使用温度范围。但Tg值高并不等于基板的耐热性能优良,而仅提高基板Tg值,尚不能完全满足有热态性能要求和高尺寸稳定性要求的电子电路组装要求。因此FR-5型覆铜板及耐高热要求覆铜板应运而生。当前,被用于耐高热覆铜板生产的主要有聚酰亚胺树脂,三嗪树脂、BT树脂等。上述树脂覆铜板工艺性能远不如环氧树脂,像聚酰亚胺树脂及三嗪树脂热压成型温度较高,这就必须提高层压机使用温度范围,即层压机设计时要考虑当产品压制温度超过200℃时,热压板须提供更高温度,此时要考虑热压板与液压缸之间的隔热层,热压板传热对机架精度稳定性影响,包括热压板材质等都得重新设计,热源需重新选定等问题。即其覆铜板生产工艺性及基板层间结合力、树脂与铜箔结合力远不如环氧树脂优良。所以,当产品对耐热要求在180℃以内产品,更多地使用FR-5型产品。
FR-5型覆铜板主要特点是特态下仍能保持优良性能,包括机械性能和较高尺寸稳定性。当PCB板既薄,又进行裸芯片等高密度组装时,对基板的机械强度及耐热性有更高要求。用普通FR-4型覆铜板或一般提高Tg FR-4型覆铜板已不能充分满足其使用需要。FR-5型覆铜板树脂配方,选用含芳香基多官能环氧树脂及含芳香基固化剂,大大提高了体系的耐热性与刚性。使产品的机械特性,特别是在高温下机械特性及高温下电性能明显高于FR-4型覆铜板。FR-5型覆铜板典型配方见表7-2-1。当树脂体系中芳香基比例提高了以后,基板层间粘合力,树脂与铜箔粘合力,基板在PCB制程加工性钻孔排屑性就会下降。在树脂配方筛选时应充分留意。 |
|
|
|
|
|
|
热点新闻 |
|
|
|